2025 Author: Erin Ralphs | [email protected]. Last modified: 2025-01-22 21:14
Clutch is an integral part of any modern car. It is this node that takes on all the colossal loads and shocks. Particularly high voltage is experienced by devices on cars with a manual transmission. As you already understood, in today's article we will consider the principle of operation of the clutch, its design and purpose.
Element characteristic
The clutch is a power clutch that transfers torque between the two main components of the car: the engine and gearbox. It consists of several disks. Depending on the type of force transmission, these clutches can be hydraulic, friction or electromagnetic.
Destination
Automatic clutch is designed to temporarily disconnect the transmission from the engine and smoothly grind them. The need for it arises as the movement begins. Temporary disconnection of the engine and gearbox is also necessary during subsequent gear changes, as well as during sudden braking and stopping the vehicle.
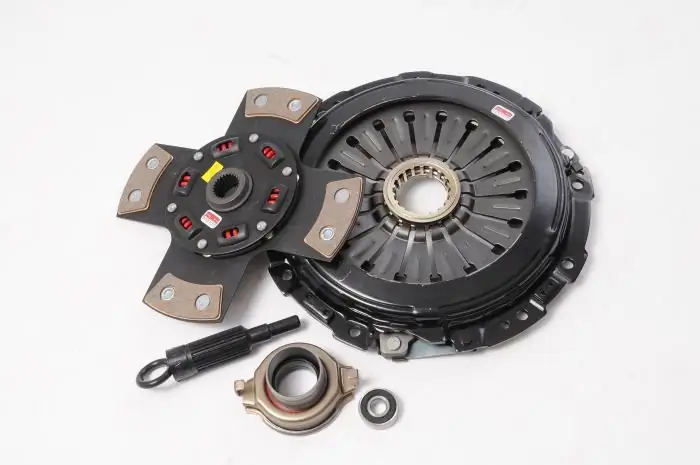
When the machine is moving, the clutch system is mostly engaged. At this time, it transfers power from the engine to the gearbox, and also protects the gearbox mechanisms from various dynamic loads. Those that arise in the transmission. Thus, the load on it increases as the engine decelerates, with a sharp engagement of the clutch, a decrease in the crankshaft speed, or when the vehicle hits road irregularities (pits, potholes, and so on).
Classification by connection of driving and driven parts
Clutch is classified according to several criteria. According to the connection of the leading and driven parts, it is customary to distinguish between the following types of devices:
- Friction.
- Hydraulic.
- Electromagnetic.
By type of push force generation
On this basis, types of clutch are distinguished:
- With central spring.
- Centrifugal.
- With peripheral springs.
- Semi-centrifugal.
According to the number of driven shafts, the systems are single-, double- and multi-disk.
By drive type
- Mechanical.
- Hydraulic.
All of the above types of clutches (with the exception of centrifugal) are closed, that is, constantly turned off or on by the driver when shifting gears, stopping and braking the vehicle.
At the moment, friction type systems have gained great popularity. These nodes are used ascars and trucks, as well as buses of small, medium and large class.
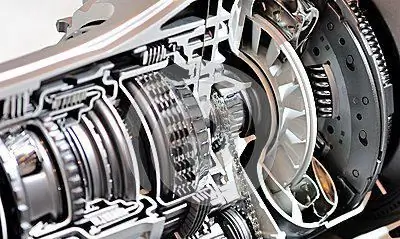
2-disc clutches are only used on heavy duty tractors. They are also installed on large-capacity buses. Multidisk is practically not used by automakers at the moment. Previously, they were used on heavy trucks. It is also worth noting that hydraulic couplings as a separate unit on modern machines will not be used. Until recently, they were used in car boxes, but only in conjunction with a series-installed friction element.
As for electromagnetic clutches, they are not widely used in the world today. This is due to the complexity of their design and expensive maintenance.
How a mechanical clutch works
It is worth noting that this unit has the same principle of operation, regardless of the number of driven shafts and the type of pressure force generation. The exception is the drive type. Recall that it is mechanical and hydraulic. And now we will look at the principle of operation of the clutch with a mechanical drive.
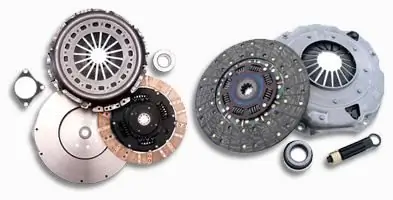
How does this node work? In working condition, when the clutch pedal is not affected, the driven disk is sandwiched between the pressure and the flywheel. At this time, the transfer of torsional forces to the shaft is carried out due to the friction force. When the driver presses the foot on the pedal, the clutch cable moves in the basket. Next, the lever rotates relative toyour place of attachment. After that, the free end of the fork begins to put pressure on the release bearing. The latter, moving to the flywheel, is to put pressure on the plates that move the pressure plate. At the moment, the driven element is released from the pressing forces and thus the clutch is disengaged.
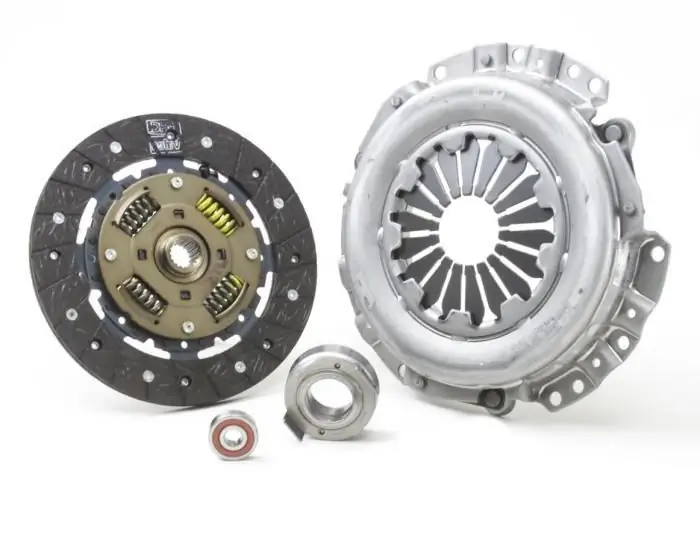
Next, the driver freely shifts gears and begins to smoothly release the clutch pedal. After that, the system reconnects the driven disk with the flywheel. As the pedal is released, the clutch engages, the shafts are lapped. After a while (a couple of seconds), the assembly begins to fully transmit torque to the engine.
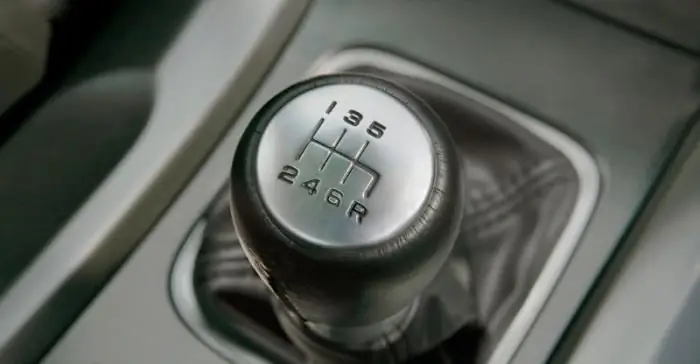
The latter drives the wheels through the flywheel. It is worth noting that the clutch cable is present only on mechanically driven units. We will describe the design nuances of another system in the next section.
How a hydraulic clutch works
Here, unlike the first case, the force from the pedal to the mechanism is transmitted through the fluid. The latter is contained in special pipelines and cylinders. The device of this type of clutch is somewhat different from the mechanical one. On the splined end of the drive shaft of the transmission and the steel casing attached to the flywheel, 1 driven disk is installed.
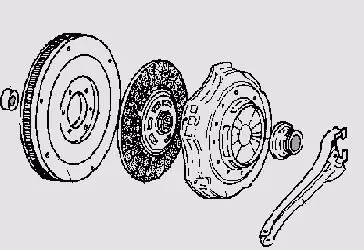
Inside the casing there is a spring with a radial petal. It serves as a release lever. The control pedal is suspended on the axis to the bracketbody. It also has an articulated master cylinder tappet attached to it. After the unit is disengaged and the gear is shifted, the spring with radial petals returns the pedal to its original position. By the way, the clutch diagram is shown in the photo on the right.
But that's not all. The design of the assembly contains both the main and the slave cylinder of the clutch. In their design, both elements are very similar to each other. Both consist of a body, inside of which there is a piston and a special pusher. As soon as the driver presses the pedal, the clutch master cylinder is activated. Here, with the help of a pusher, the piston moves forward, due to which the pressure inside increases. Its subsequent movement leads to the fact that the liquid penetrates into the working cylinder through the discharge channel. So, thanks to the impact of the pusher on the fork, the unit is turned off. At the time when the driver starts to release the pedal, the working fluid flows back. This action will engage the clutch. This process can be described as follows. First, the check valve opens, which compresses the spring. Next comes the return of fluid from the working cylinder to the master. As soon as the pressure in it becomes less than the pressing force of the spring, the valve closes, and excess fluid pressure is formed in the system. This is how all the gaps that are in a certain part of the system are leveled.
What is the difference between the two drives?
The main advantage of mechanically driven systems is the simplicity of design and low maintenance. However, unlike their counterparts, they have a lower efficiency.
Hydraulic clutch (its photo is shown below), due to its high performance, provides smoother engagement and disengagement of nodes.
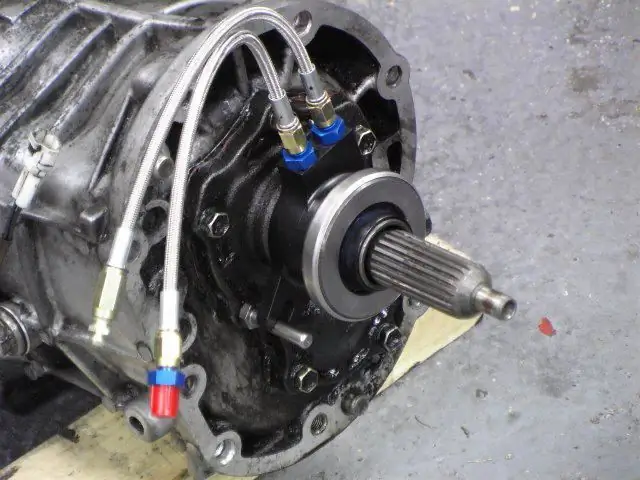
However, this type of nodes is much more complex in design, which is why they are less reliable in operation, more whimsical and costly to maintain.
Clutch requirement
One of the main indicators of this node is a high ability to transmit torque forces. To assess this factor, such a concept as “the value of the coefficient of adhesion reserve” is used.
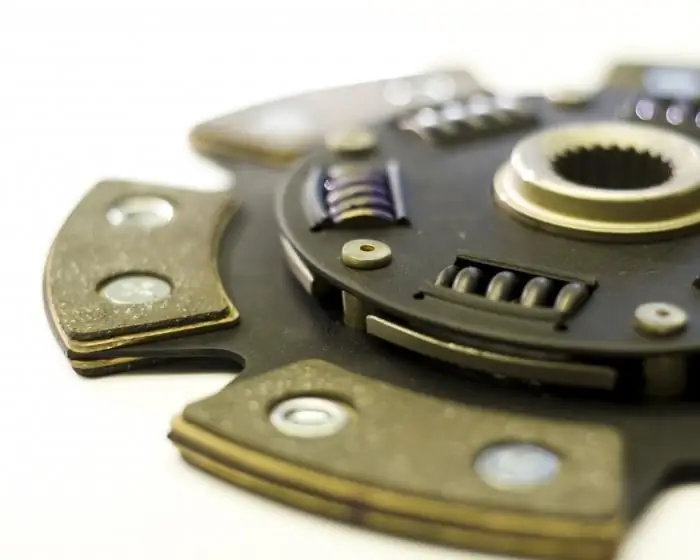
But, in addition to the main indicators that relate to each node of the machine, this system has a number of other requirements, among which it should be noted:
- Smooth inclusion. During the operation of the vehicle, this parameter is ensured by qualified control of the elements. However, some design details are designed to increase the degree of smooth engagement of the clutch assembly even with minimal driver skill.
- "Purity" shutdown. This parameter implies full shutdown, in which the torque forces on the output shaft correspond to zero or close to zero.
- Reliable transmission of power from the transmission to the engine in all modes of operation and operation. Sometimes, with an underestimated value of the safety factor, the clutch starts to slip. What leads to increasedheat and wear of machine parts. The higher this coefficient, the greater the mass and dimensions of the node. Most often, this value is about 1.4-1.6 for cars and 1.6-2 for trucks and buses.
- Ease of control. This requirement is generalized for all controls of the vehicle and is specified in the form of a characteristic of the pedal travel and the degree of effort required to completely disengage the clutch. At the moment, in Russia there is a limit of 150 and 250 N for cars with and without drive amplifiers, respectively. The pedal travel itself often does not exceed 16 centimeters.
Conclusion
So, we have considered the device and the principle of operation of the clutch. As you can see, this node is of great importance for the car. The he alth of the entire vehicle depends on its performance. Therefore, you should not break the clutch by abruptly removing your foot from the pedal while driving. In order to preserve the details of the assembly as much as possible, it is necessary to release the pedal smoothly and not to practice long shutdowns of the system. So you will ensure long and reliable operation of all its elements.
Recommended:
Double clutch: device and principle of operation
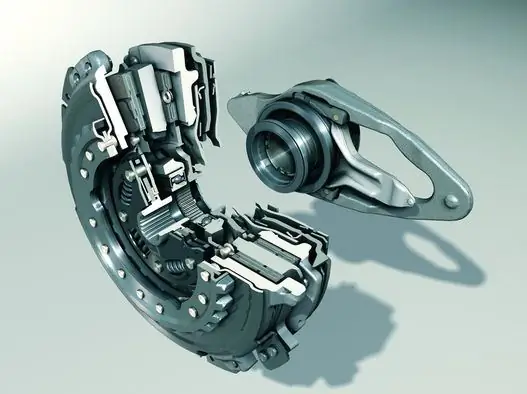
Along with the new trends in the development of "green" technologies, the automotive industry is currently experiencing no less interesting changes in terms of approaches to the development of traditional structural parts of the car. This applies not only to the design of the internal combustion engine and the inclusion of more reliable materials, but also to the control mechanics
Overrunning clutch: principle of operation, device, application
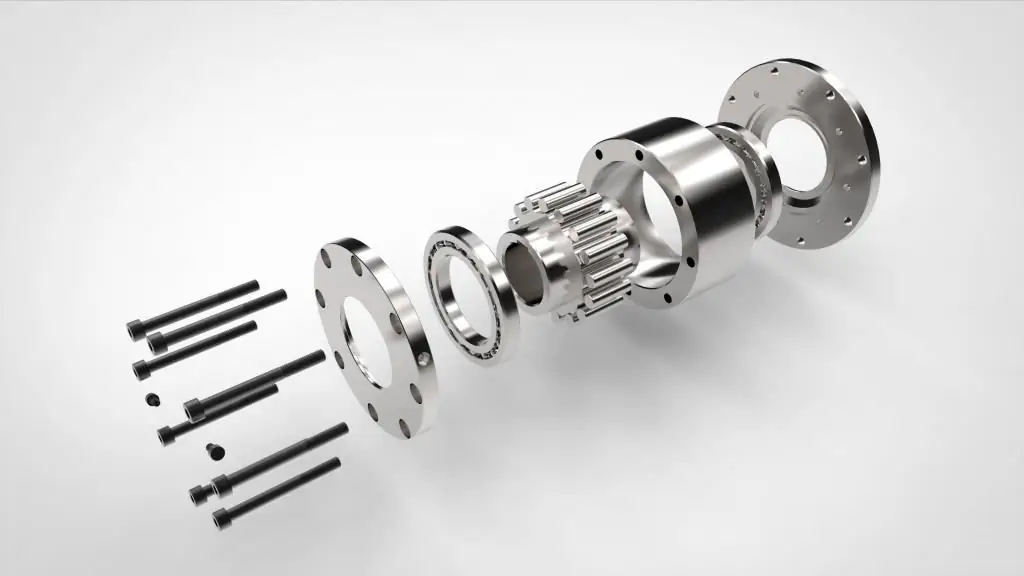
The classic freewheel is widely used in the automotive industry. The smooth functioning of the entire system depends on the quality of this unit. If the user knows how the freewheel works, he can provide optimal operating conditions to avoid premature failure of the device
Clutch master cylinder. "Gazelle": device and repair of the clutch master cylinder

To set the car in motion, it is necessary to transmit torque from the engine to the gearbox. Clutch is responsible for this
The principle of operation of the variator. Variator: device and principle of operation
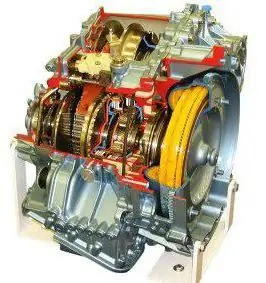
The beginning of the creation of variable programs was laid in the last century. Even then, a Dutch engineer mounted it on a vehicle. After such mechanisms were used on industrial machines
Clutch cylinder VAZ-2107: device, principle of operation, replacement and repair
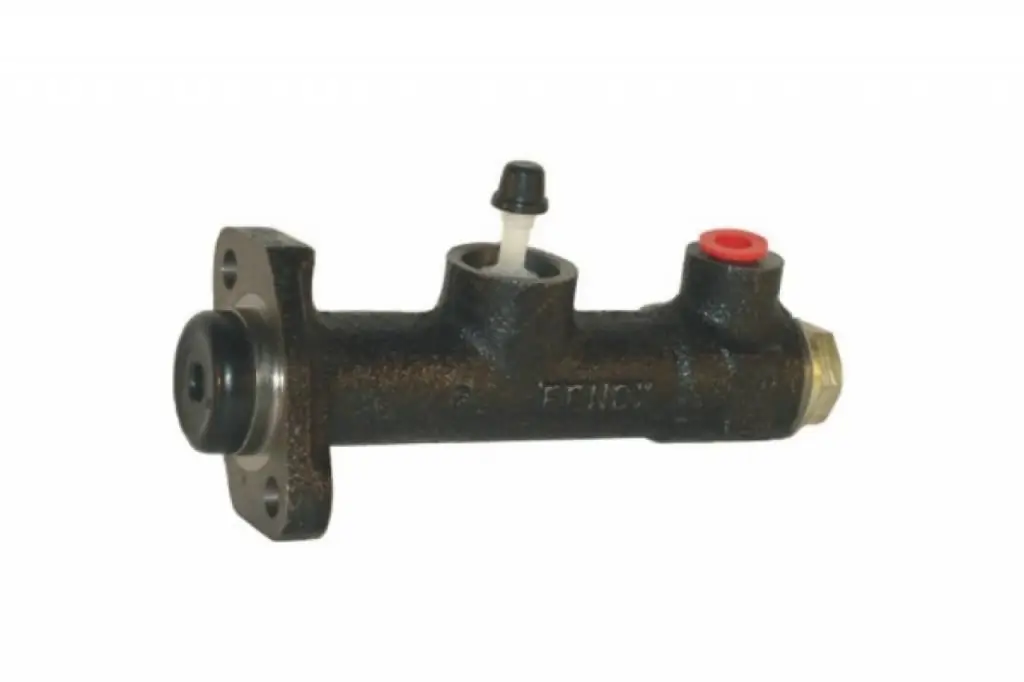
The use of hydraulic drive in the "seven" is caused by the design features of its clutch. It not only transfers force to the driven disk, but also allows the car to start off smoothly. True, this somewhat complicated the design of the car and its operation. Therefore, it is necessary to know how the VAZ-2107 clutch cylinder is arranged, the principle of its operation and operating features