2025 Author: Erin Ralphs | [email protected]. Last modified: 2025-01-22 21:14
The demands placed on modern diesel engines in terms of power, efficiency and environmental friendliness are becoming ever higher. To meet these requirements, good mixture formation must be ensured. To do this, the engines are equipped with modern and efficient fuel injection systems. They are able not only to provide the finest spray due to higher pressure, but also to regulate the injection moment and the amount of fuel supplied to the cylinders with high accuracy. Such a system exists and fully satisfies all those high requirements. This is a diesel engine injector. It is a separate injection element for each cylinder in the engine. The part is controlled by an electronic unit.
Diesel Ideas
About the creation of a node in which the nozzle and the fuel pump would be combined,thought himself the creator of these engines - Rudolf Diesel.
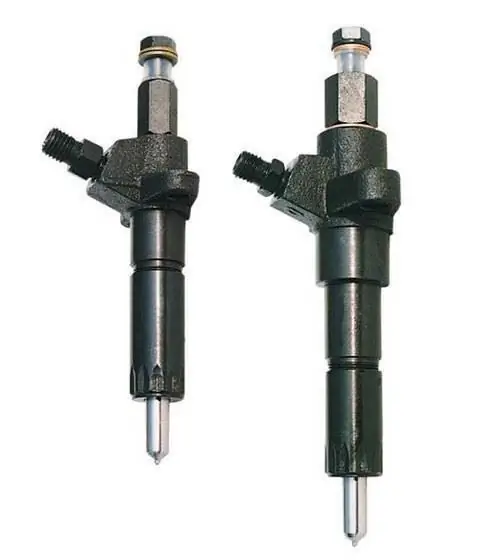
This would allow you to get away from the fuel lines and high pressure pipelines, thereby increasing the injection pressure. But in the days of Diesel, the opportunities that exist today did not yet exist.
System Description
The diesel engine injector pump is a fuel supply pump and injector, which is combined in one unit. As in injection pumps with nozzles, injection based on these elements can perform certain tasks. The system creates sufficient pressure, supplies a certain portion of the fuel mixture at the right time. There is a separate pump for each combustion chamber. That is why now you can find engines where there are no high-pressure fuel lines, which are on power units with high-pressure fuel pumps.
Historical facts
This injection system is not a new development. The diesel engine injector was installed on cars in the late 30s. For the first time, the design was tested on diesel engines for railway, marine, and also trucks. All this technique was united by one thing - low speed. The features of these engines are the presence of a separate pump for each cylinder and short pressure lines that go to the nozzle. The elements are driven by pushers and buffers.
Serially began to use such systems on trucks since 1944. On passenger cars - since 1988. In 1938, the Detroit Diesel Company, which then belonged to the GeneralMotors, the first such unit was created, in which a diesel engine power system with pump nozzles was used. Despite the fact that the device was developed in the USA, designs of this type were also developed in the USSR.
The first YaAZ-204 engines were equipped with such nozzles already in 1947. But these units were produced under the license of Detroit-Diesel. This power unit, and then a modified six-cylinder engine, was produced until 1992.
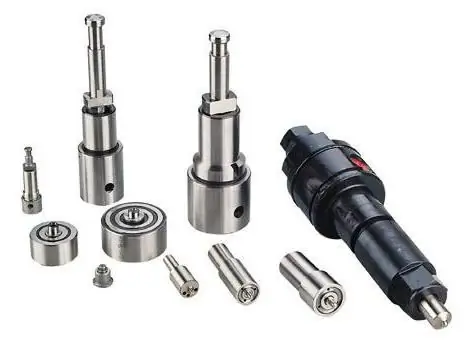
In 1994, the device and operation of the diesel engine injector were noticed by Volvo engineers. The company produces the first truck FH12 with nozzles of this type. Then they will start equipping their Scania and Iveco trucks with the same units.
Among passenger cars, this system was first used on Volkswagens. The Volkswagen diesel engine injector appeared in 1998. In the late 90s, engines with such a system occupied 20% of the automotive market.
Device
So, let's consider what a diesel engine injector is. Its device is extremely simple. In the body of the unit there is directly the nozzle, the dosing unit, as well as the power unit. Thanks to this power drive, the unit injector has certain advantages over traditional systems. Thus, the time of movement of a flammable liquid under high pressure is significantly reduced. It also increases hydraulic efficiency and reduces weight.
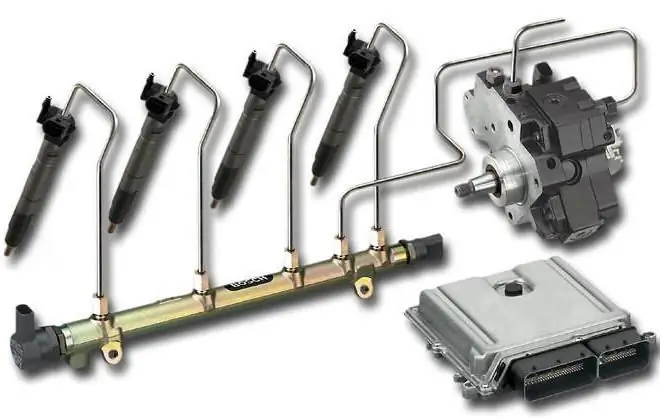
The latest generation nozzles are equipped with pumps capable of delivering sufficiently high pressure (up to 2,500 bar). They can instantly respond to commands from the ECU, which collects and analyzes current information from external sensors. Based on these data, the required amount of the mixture and the injection time are determined. This makes it possible to obtain optimal power values for given operating conditions. In addition, the units help save diesel fuel, which minimizes harmful emissions into the atmosphere and helps reduce noise from a running engine. And finally, the device is very compact and can be placed in the cylinder head. You can also install other parts and assemblies there.
The nozzle is designed to provide the most efficient mixture formation. For this, engineers have provided for phases - this is a preliminary, main and additional injection. Preliminary gives smooth combustion at the moment of the main phase, when high-quality formation of the working mixture is ensured in different engine operating modes. An additional one is required for regeneration processes in the particulate filter.
Mechanical injector principle
The diesel engine injector is installed directly in the cylinder head. There are four special cams on the camshaft. They serve to start the injector drive. With the help of rocker arms, the force is transmitted to the pump-injectors by means of plungers.
The drive cam has a special profile that provides a sharp rise up, and then a slow lowering of the rocker. When the last risesthe plunger is quickly pressed down. This creates the right pressure. When slowly lowering the rocker down, the plunger goes up. This allows the fuel to enter the high pressure chambers without air bubbles.
The injection process itself takes place when control voltage is applied from the ECU to the solenoid valve.
Injection phases
Let's take a closer look at the principle of operation of the diesel engine injector. When, under the influence of the rocker, the plunger moves down, the combustible mixture flows through the channels into the nozzles. When the valve closes, the diesel flow is cut off. The pressure starts to rise. When it reaches a level of 13 MPa, the spray needle will overcome the spring force. After that, the pre-injection phase will begin.

As soon as the valve begins to open, the pre-phase ends and the fuel mixture is directed through the supply line. The pressure starts to drop. Depending on the engine operating mode, one or two preliminary phases can be performed.
When the plunger moves down, the main injection stroke begins. The valve closes again, the fuel pressure rises again. Upon reaching a level of 30 MPa, the spray needle will overcome the pressure force and rise up, thereby starting the injection process. The higher the pressure rises, the more fuel will be compressed. The amount of diesel and air that can enter the cylinder is increased.
Maximum feed (and it is carried out when the motor is running in peak modepower), is carried out at a pressure of 220 MPa. The opening of the valve completes the main injection stage. Pressure drops, needle closes.
An additional injection phase is performed when the plunger further moves down. The principle of operation of the device at this stage is the same as the main injection. More often, the algorithm is performed in two stages.
If we consider the device of the pump-injector of a TDI diesel engine, then it can be equipped with a sensor that monitors the lifting of the needle. The position of the needle is needed by the control unit, where the fuel pumps are also electronically controlled.
Benefits
While the common rail system uses battery injection, the unit injector delivers the fuel mixture at a higher pressure due to the absence of long lines.
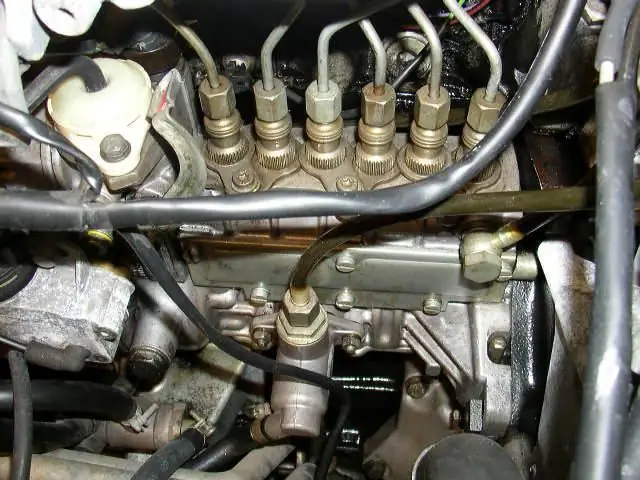
They can often be destroyed during the operation of the car. This is the weak link in classical power systems. The pump injector allows more fuel to be fed into the combustion chamber. This will make spraying more efficient. Motors equipped with such units are more powerful.
In addition, engines with this type of injection are less noisy than their counterparts. But with the Common Rail or injection pump, the pump injector will still be more compact.
Flaws
But there are also disadvantages. The most serious disadvantage is the high demands on the quality of fuel. The slightest blockage is enough for the system to stop working. The second negative is the price.
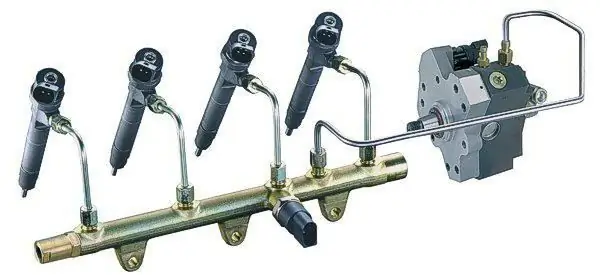
It is almost impossible to repair this exact assembly outside the factory. Another drawback is that when exposed to high pressure, these nodes often break the landing sockets in the engine block.
How to maintain the pump injector?
As you can see, these nodes are very demanding on the quality of diesel, and it is far from high in our country and in the CIS. In order not to have to change this expensive element often, it is recommended to regularly change fuel, air and all other filters, purchase original consumables.
About flushes
Often, car owners are interested in how to flush the injector pump on a diesel engine. Experts do not recommend flushing - this is not good for any nozzle. It is better to change the filters and refuel at proven gas stations.
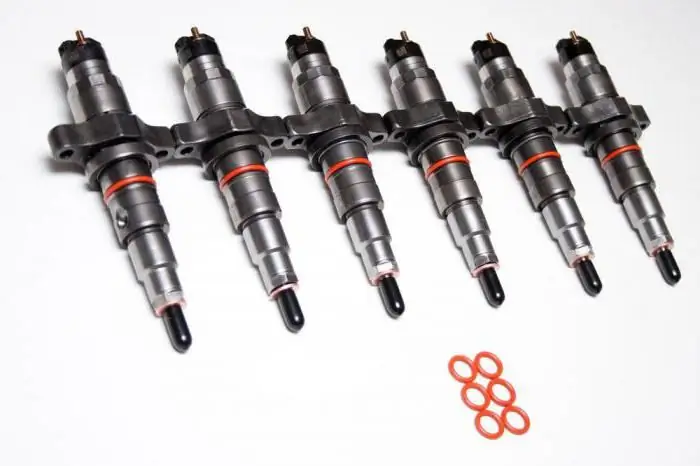
Flushing on the bench is suitable if there is poor quality atomization - unstable idling and similar problems. Rinse in an ultrasonic bath is allowed when the needle is completely stuck. If the nozzle is pouring, then nothing will help here. For washing, you can use the currently popular LAVR and VINS products.
In general, if an injector is not working, it is best to have it serviced and replace parts that are out of order. Flushing helps only if the node somehow works.
Conclusion
So, we found out what a diesel engine injector is and what its device is. As you can see, this is an integral element of the diesel engine power supply system. He hasmore technologically advanced design, but very demanding on fuel quality.
Recommended:
The principle of operation of the variator. Variator: device and principle of operation
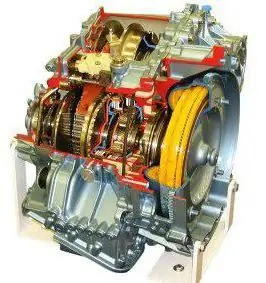
The beginning of the creation of variable programs was laid in the last century. Even then, a Dutch engineer mounted it on a vehicle. After such mechanisms were used on industrial machines
"Lada-Kalina": ignition switch. Device, principle of operation, installation rules, ignition system, advantages, disadvantages and features of operation
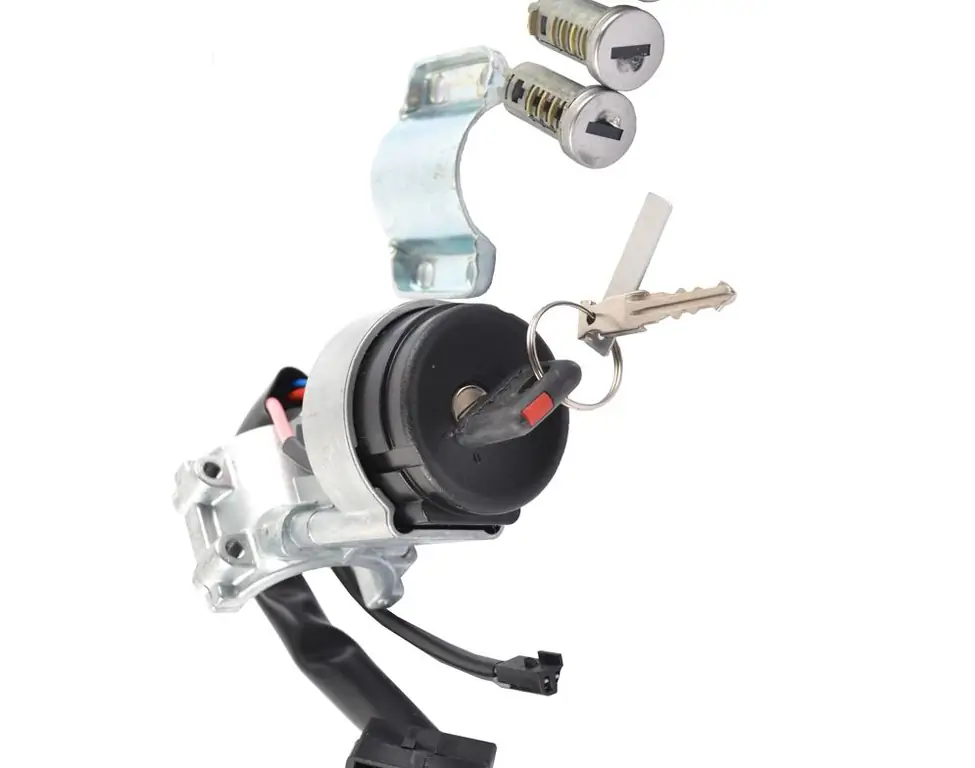
Detailed story about the ignition switch Lada Kalina. General information and some technical characteristics are given. The device of the lock and the most frequent malfunctions are considered. The procedure for replacing with your own hands is described
What is diesel? The principle of operation, device and technical characteristics of the diesel engine
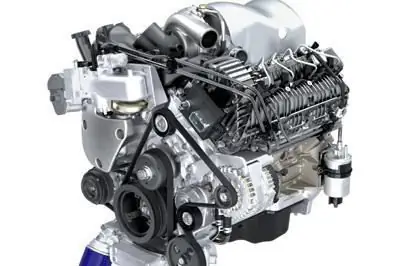
Diesel engines are the second most common type of engine in passenger cars. This is primarily due to such characteristics and features as high-torque power and efficiency, which a diesel engine has
Planetary gearbox: device, principle of operation, operation and repair
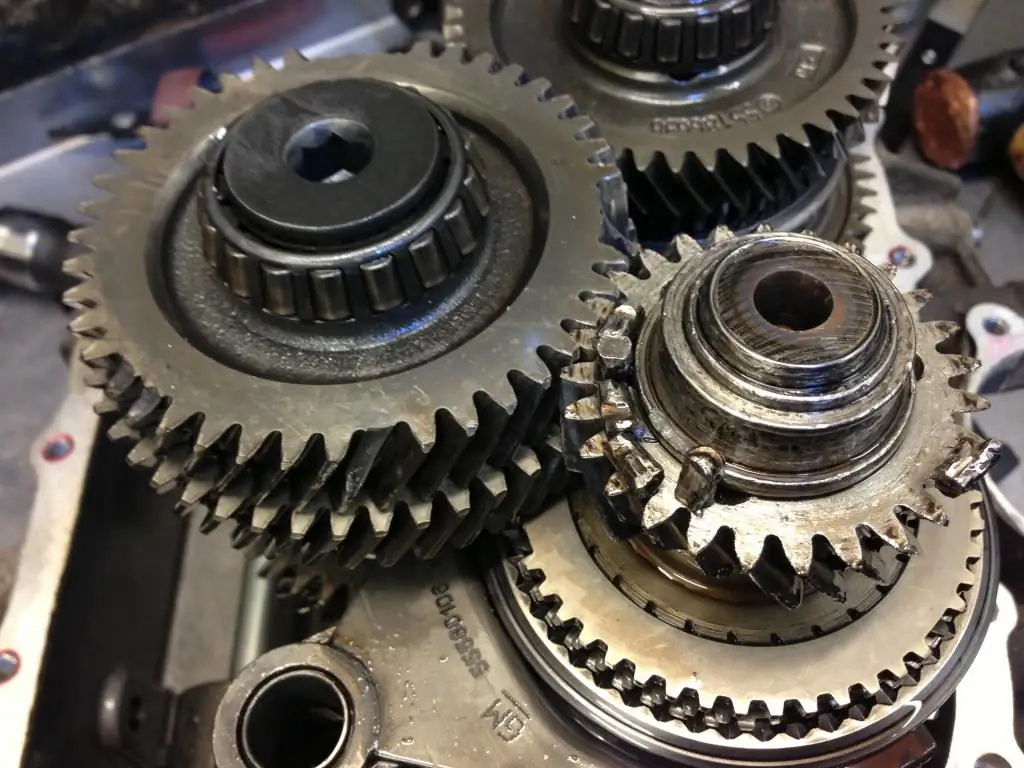
Planetary gears are among the most complex gear boxes. With a small size, the design is characterized by high functionality, which explains its widespread use in technological machines, bicycles and caterpillar vehicles. To date, the planetary gearbox has several design versions, but the basic principles of operation of its modifications remain the same
Carburetor and injector: difference, similarities, advantages and disadvantages of carburetor and injection engines, principle of operation and expert reviews

For more than a hundred years, the car has firmly established itself in our lives. During this time, managed to become a familiar, everyday means of transportation. Let's see what the difference is between a carburetor and an injector, what advantages and disadvantages they have