2025 Author: Erin Ralphs | [email protected]. Last modified: 2025-01-22 21:14
The starter motor, or "starter", is a 10 horsepower carburetor-type internal combustion engine used to help start diesel tractors and machinery. Similar devices were previously installed on all tractors, but today a starter has come to replace them.
Starting motor device
The design of the PD consists of:
- Power systems.
- Reducer starting motor.
- Crank mechanism.
- Skeins.
- Ignition systems.
- Regulator.
The engine frame consists of a cylinder, a crankcase and a cylinder head. The parts of the crankcase are bolted together. The pins outline the center of the starting motor. The transmission gears are protected by a special cover and are located in the front of the crankcase, the cylinder is in the upper part. Doubled cast walls create a jacket into which water is supplied through a pipe. Wells connected by two purgewindows, allow the mixture to flow into the crankcase.
According to their design, starting engines are two-stroke starting engines paired with modified diesels. The engines are equipped with a single-mode centrifugal governor directly connected to the carburetor. The stability of the crankshaft, as well as the opening and closing of the throttle valve, are automatically regulated. Despite the low power (only 10 horsepower), PD can rotate the crankshaft at a speed of 3500 rpm.
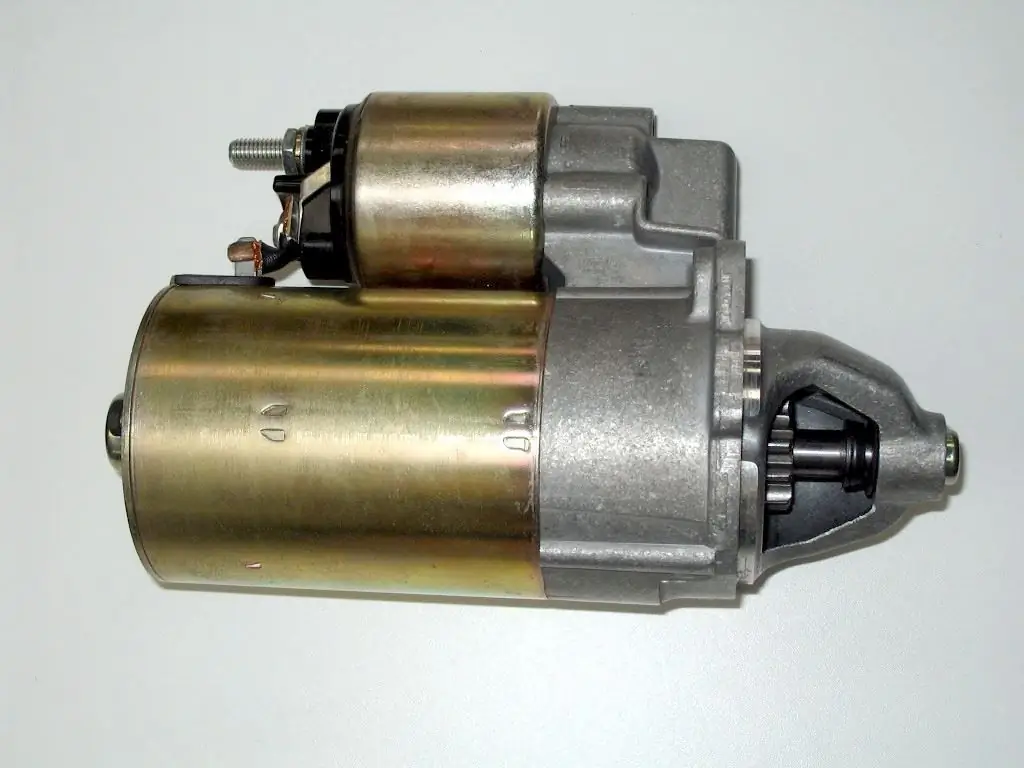
The principle of operation of the starting motor
The starter, like most single-cylinder two-stroke engines, runs on gasoline. The PD is equipped with spark plugs, high voltage wires and an electric starter.
The principle of operation of the engine is as follows:
- The piston, during the transition of the distance between the bottom and top dead center, first closes the purge window, and then the inlet.
- The combustible mixture that has entered the combustion chamber during this time is under pressure.
- The vacuum that appears at this moment in the crank mechanism transfers the combustible mixture from the carburetor to the crank chamber after the piston opens the inlet window.
- Ignition of fuel with a spark occurs at the moment when the piston is near TDC. Parts are lubricated by spraying fuel, which is mixed in a 1:1 ratio with oil.
Simple design of starting motors (PD) allows the use of fuel and oilthe lowest quality. The launcher is turned on by pressing the button located on its body.
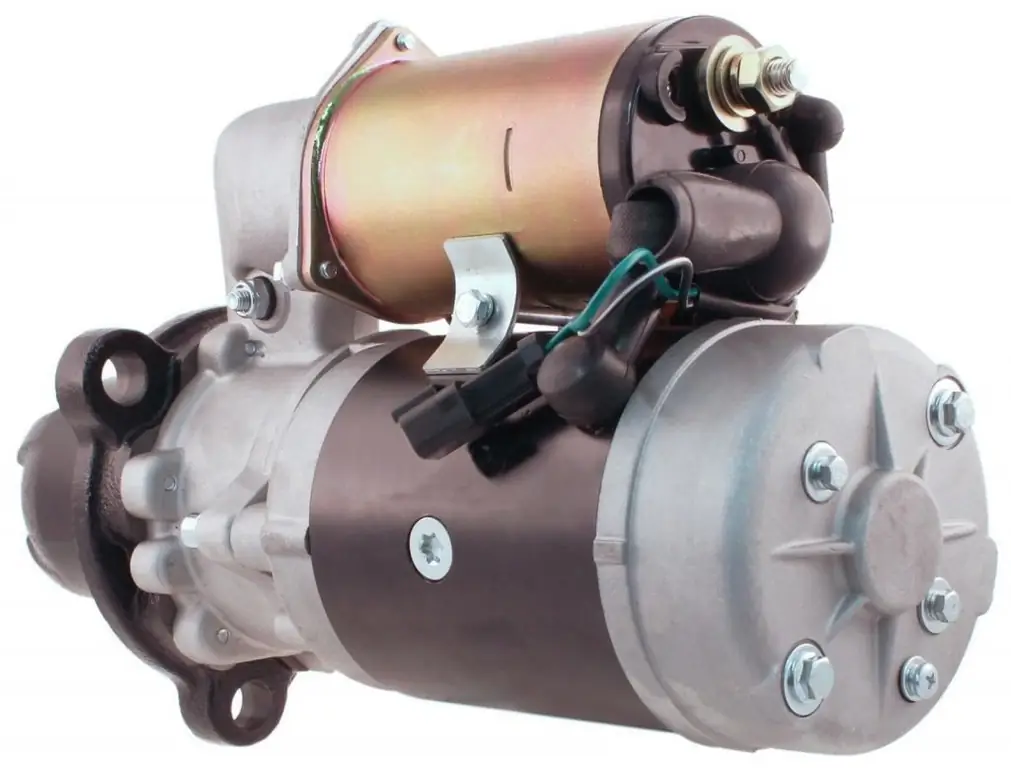
PD Models
Some models of launchers are still used on tractors and special equipment of various brands and models.
- PD-8. Single-cylinder two-stroke engine with a power of 5.1 kW. The crankshaft speed is 4300 rpm. The fuel mixture is formed externally using a carburetor. The diameter and stroke of the cylinder are the same and are 62 millimeters, the working volume is 0.2 liters. The fuel compression ratio is 6, 6. The fuel used is a mixture of diesel oil and gasoline in a ratio of 1:15.
- PD-10. Single-cylinder two-stroke engine with crank-chamber scavenging. The mixture formation is external, using a carburetor. The stroke of the cylinder is 85 millimeters, the diameter is 72 millimeters, and the volume is 0.346 liters. Torque - 25 N/m, fuel compression ratio - 7.5.
- P-350. Single-cylinder two-stroke starting engine with crank-chamber purge. The formation of the mixture is carburetor. The stroke of the cylinder is 85 millimeters, the diameter is 72 millimeters, the volume of the cylinder is 0.364 liters. Torque 25 N/m, compression ratio 7.5.
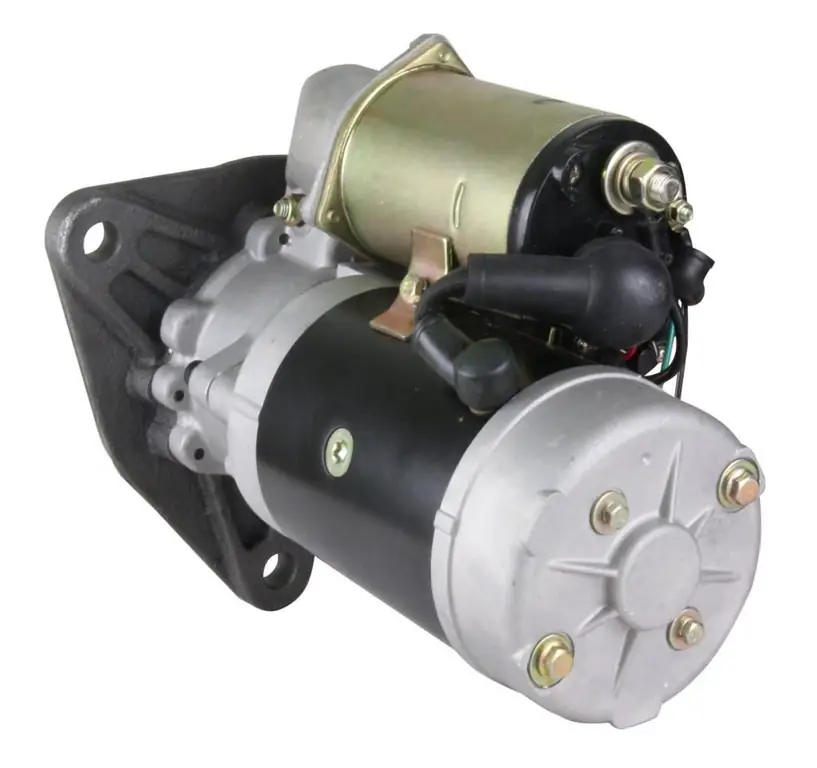
Common problems and solutions
If the starting motor fails to start, diagnose the problem and try to fix it. The reason for this may be clogging of the main mechanisms and engine parts, which prevents fuel from enteringinto the float chamber. You can fix this by cleaning all parts.
The lack of spark at the end of the plug can be another reason why the engine does not start. In this case, the wiring passing through the magneto is checked. Knocked down adjustment is corrected after starting and warming up the engine. An incorrectly set ignition timing may be one of the reasons that the PD does not start.
Incorrect engine operation can be caused by several reasons:
- The idle jet was clogged.
- Idle screw set incorrectly.
- Main jet dirty.
- Incorrect ignition angle setting.
- Throttle opening problems.
- Clogged pipeline.
- Clogged motor start capacitor.
Rapid overheating of the engine is eliminated by adding water, but there may be several reasons for heating - for example, clogging of the space between the head and the cylinder or the combustion chamber with soot. This is eliminated by cleaning all the mechanisms of the switched off engine. However, the cause of the launcher overheating is not always the lack of water or contamination: initially it is designed for a maximum of 10 minutes of operation at a time. Longer use may cause it to wear out faster.
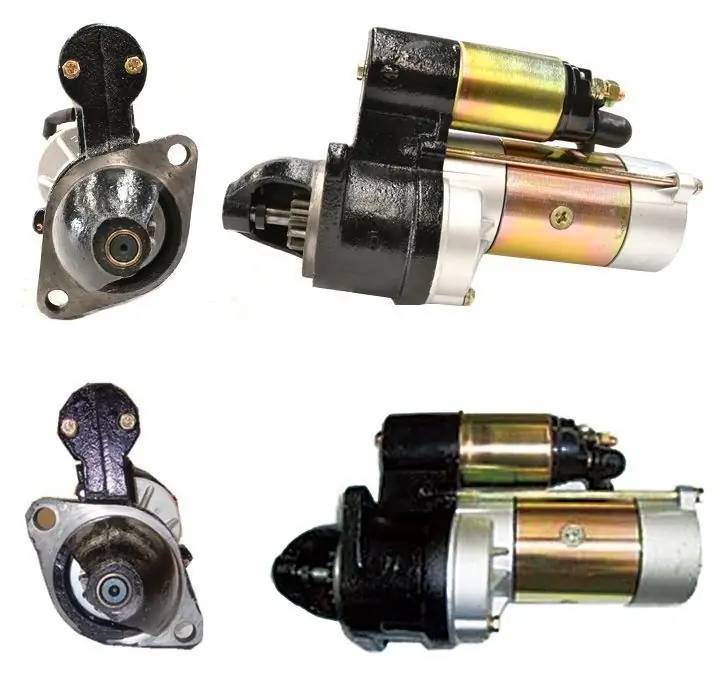
Adjustment and tuning of PD
Stable and correct operation of the launcher is possible only if all mechanisms and parts are properly configured. First, the carburetor is tuned by setting the length of the rod,combining the throttle lever and the regulator. Carburetor adjustment is carried out at low speeds.
The next step is to set the crankshaft speed using a spring. Changing its compression level allows you to adjust the number of revolutions. The ignition system and the drive gear disengagement mechanism are the last to be adjusted.
Engine PD-10
The main part of the PD-10 design is a cast-iron crankcase assembled from two halves. A cast-iron cylinder is attached to the crankcase by means of four studs, a carburetor is attached to the front wall of which, and a silencer is attached to the rear wall. The cast-iron head closes the cylinder from above, the ignition spark plug is screwed into the central hole. The sloping hole, or faucet, is designed to purge the cylinder and fill fuel.
The crankshaft is placed on ball bearings and roller bearings in the inner cavity of the crankcase. The gear is mounted on the front end of the crankshaft, and on the rear - the flywheel. Self-locking oil seals seal the exit points of the crankshaft from the crankcase. The crankshaft itself has a composite structure.
The power system is represented by an air cleaner, a fuel tank, a carburetor, a sediment filter, a fuel line that connects the carburetor and the tank sump.
The single-phase motor with starting winding uses a mixture of diesel oil and gasoline in a ratio of 1:15 as fuel. At the same time, the mixture is used to lubricate the surfaces of rubbing engine parts.
The engine cooling system is common with diesel and iswater thermosyphon.
The ignition system is represented by a right-hand rotation magneto, wires and candles. The crankshaft gears are driven by magneto.
The electric starter provokes the starting torque of the PD-10 engine. The flywheel is connected to the starter gear with a special crown and has a groove designed to manually start the engine.
After starting, the engine with the starting winding is connected by means of a transmission mechanism to the main engine of the tractor. The transmission mechanism consists of a friction multi-plate clutch, an automatic switch, an overrunning clutch and a reduction gear. At the starting moment of the asynchronous motor, the automatic switch engages the gear with the toothed flywheel, setting the friction clutch in motion. The frequency of rotation of the crankshaft of the main engine is dialed until it starts to work independently. After that, the clutch and the automatic switch are activated. The launcher stops after an electrical circuit break.
To ensure the correct starting torque of an asynchronous engine, the fuel mixture is supplied to the cylinders of carburetor engines by the power system, on which the main engine indicators depend - efficiency, power, exhaust gas toxicity. The system must be kept in excellent technical condition during the operation of the launchers.
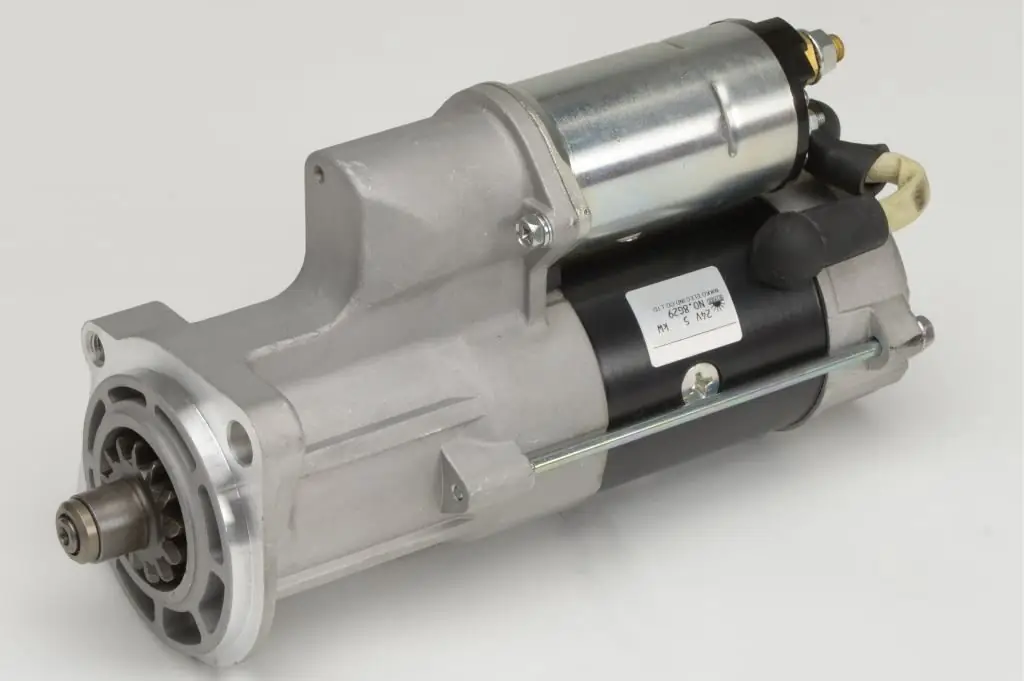
Advantages of starting internal combustion engines and requirements for them
Among the advantages of engines note the possibility of heating engine oil in the crankcase usingexhaust gases and heating the cooling system by circulating the coolant through the cooling jacket.
Carburetor engines are fundamentally different from other engines in the power system, including the fuel system and the device that provides it with air supply.
Basic requirements for carburetors:
- Quick and reliable engine start.
- Fine atomization of fuel.
- Ensure fast and reliable engine starting.
- Precise fuel metering for excellent performance and economy in all engine operating modes.
- Ability to smoothly and quickly change the engine operating mode.
PD Maintenance
Maintenance of the launcher consists in adjusting the gaps between the contacts of the magneto breaker and the electrodes of the spark plug. And also in the diagnosis and inspection of the starting working winding of the engine.
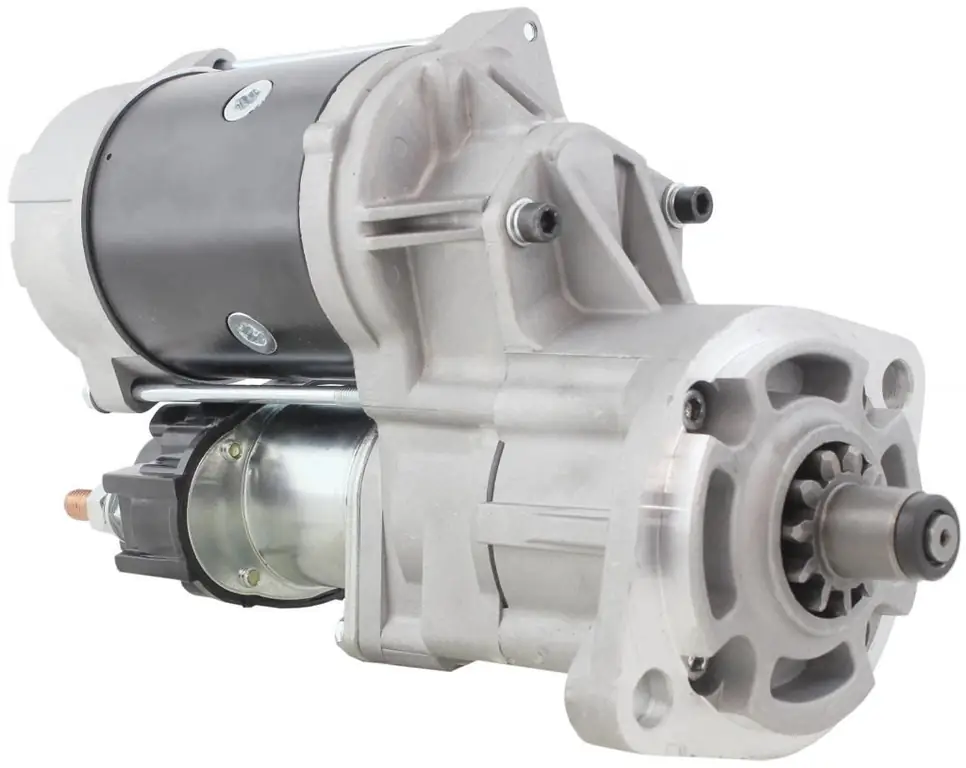
Checking gaps between electrodes
The spark plug is unscrewed, the hole is closed with a plug. The deposit on the candle is eliminated by placing it in a bath of gasoline for several minutes. The insulator is cleaned with a special brush, the body and electrodes with a metal scraper. The gap between the electrodes is checked with a probe: its value should be within 0.5-0.75 mm. The gap is adjusted by bending the side electrode if necessary.
The serviceability of the candle is checked by connecting it to the magneto with wires and scrollingcrankshaft until a spark appears. After inspection and maintenance, the spark plug is returned to its place and twisted.
Checking the gap between the breaker contacts
Breaker parts are wiped with a soft cloth soaked in gasoline. The soot formed on the surface of the contacts is cleaned with a needle file. The crankshaft of the engine scrolls to the maximum opening of the contacts. The measurement of the gap is carried out with a special probe. If it becomes necessary to adjust the gap, then with a screwdriver, the tightening of the screw and the rack fasteners are loosened. The cam wick is moistened with a few drops of clean engine oil.
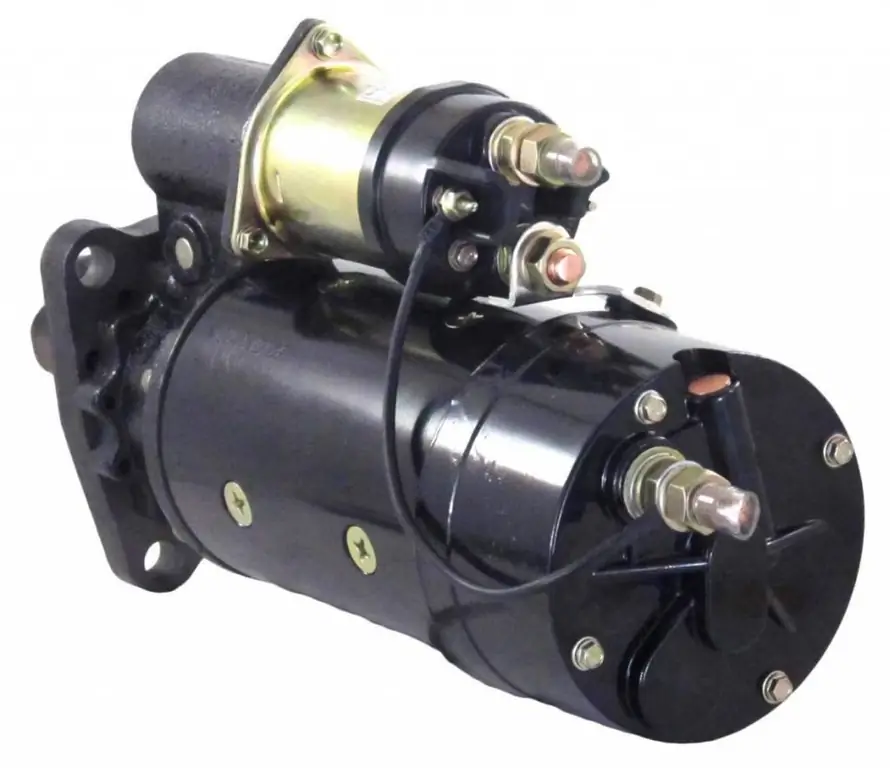
Ignition timing
The ignition timing of the starting motor is adjusted after the spark plug is removed. A caliper depth gauge is lowered into the cylinder bore. The minimum distance to the bottom of the piston is shown by a depth gauge at the moment the crankshaft turns and the piston rises to top dead center. After that, the crankshaft rotates in the opposite direction, and the piston drops below the dead center by 5.8 millimeters. The contacts of the magneto breaker must be opened by the rotor cam. If this does not happen, then the magneto rotates until the contacts open and is fixed in this position.
Gear adjustment
Maintenance of the launcher gearbox consists in its regular lubrication and adjustment of the switching mechanism. The gearbox clutch begins to slip when adjusting the engagement mechanism in case of excessive wear on the discs. Signs of this are overheating of the clutch and too slow rotation of the crankshaft at startup.
The mechanism for engaging the gearbox is adjusted when starting the starting gear by turning the lever to the right and removing the spring. Under the action of the spring, the lever returns to the leftmost position and engages the gearbox clutch. In this case, the angle between the vertical and the lever should be 15-20 degrees.
The lever is rearranged on the slots of the roller in case the angle does not correspond to the specified norm. It moves from the extreme left to the extreme right position under the action of the release spring. The position of the lever is adjusted by the traction forks so that it is in a horizontal position, after which the spring is installed. The left end of the earring slot, when properly adjusted, should be in contact with the lever pin, and the finger itself should be in contact with the right end of the earring slot with a small gap. On the earring, the marks limit the area within which the lever finger must be located when the gearbox clutch is engaged.
A properly adjusted drive ensures that the starting gear is turned on when the lever is raised to the upper limit position and the gearbox clutch is engaged when moving to the lower limit position. When the gear is turned on, the gearbox clutch must be engaged, which is a prerequisite.
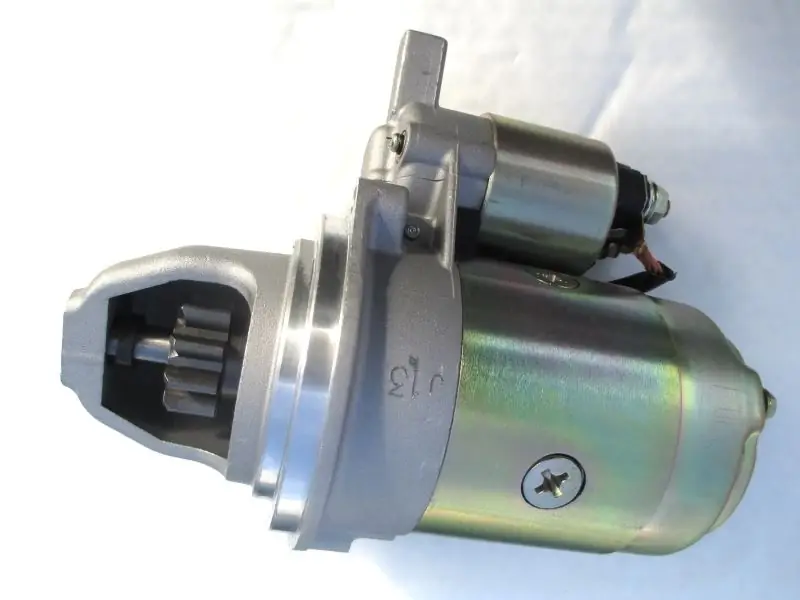
Adjusting the mechanism for engaging the gearbox
The mechanism for engaging the gearbox is adjusted by transferring the clutch control lever to the on position by turning it counterclockwise as far as it will go. The deviation of the lever from the vertical should not exceed 45-55 degrees.
To adjust the angle without changing the roller, unscrew the bolts, remove the lever from the splines and set it in the desired position, after which the bolts are tightened. The starting gear, or bendix, must be in the off position, for which the lever is turned counterclockwise without moving.
The length of the rod is adjusted with a threaded fork so that it is put on the levers. In this case, the finger of the lever of the starting gear must occupy the leftmost position of the slot. The maximum gap between the pin and the slot should not exceed 2 millimeters. The fingers are splinted after installing the rod, then the fork locknuts are tightened. The lever is returned to the vertical position and connected to the rod. The clutch adjusts the length of the rod.
After adjusting the mechanism, make sure that the lever moves without jamming. The operation of the mechanism is checked at startup. The starting gear must not grind while the starting motor is running.
With proper adjustment and tuning of all mechanisms and parts, stable operation of the engine is ensured.
Recommended:
"Peugeot Boxer": dimensions, technical characteristics, declared power, maximum speed, operating features and owner reviews
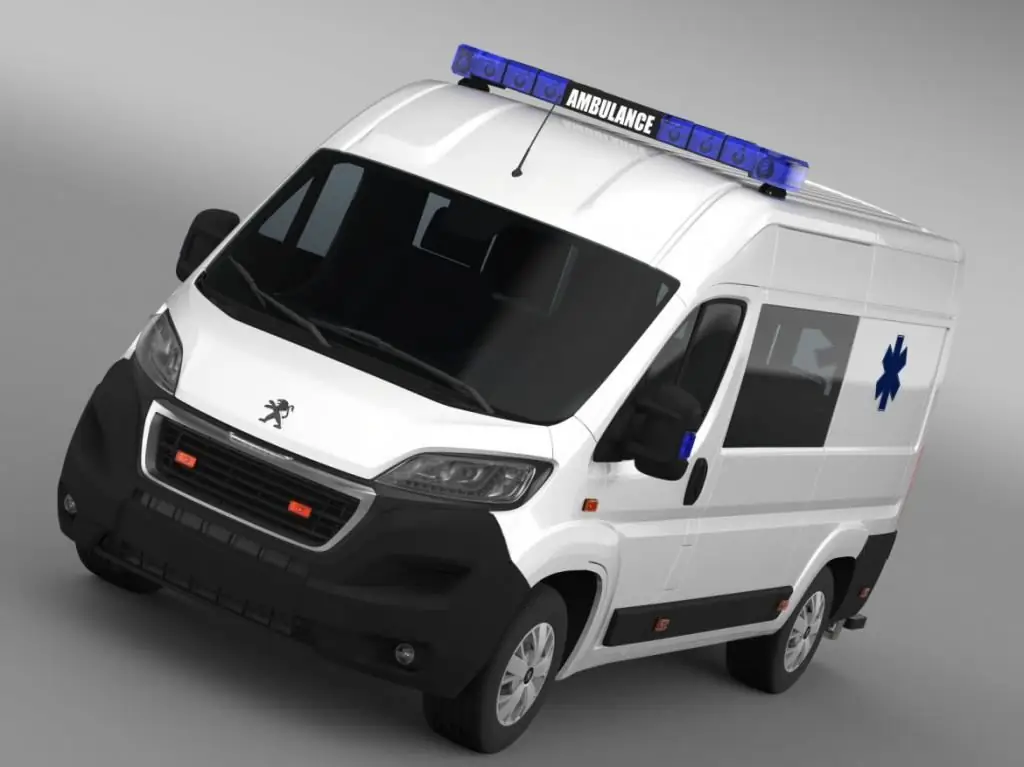
Dimension "Peugeot-Boxer" and other technical characteristics. Car "Peugeot Boxer": body, modifications, power, speed, features of operation. Owner reviews about the passenger version of the car and other models
Tractor "Buller": technical characteristics, declared power, fuel consumption, operating features and owner reviews
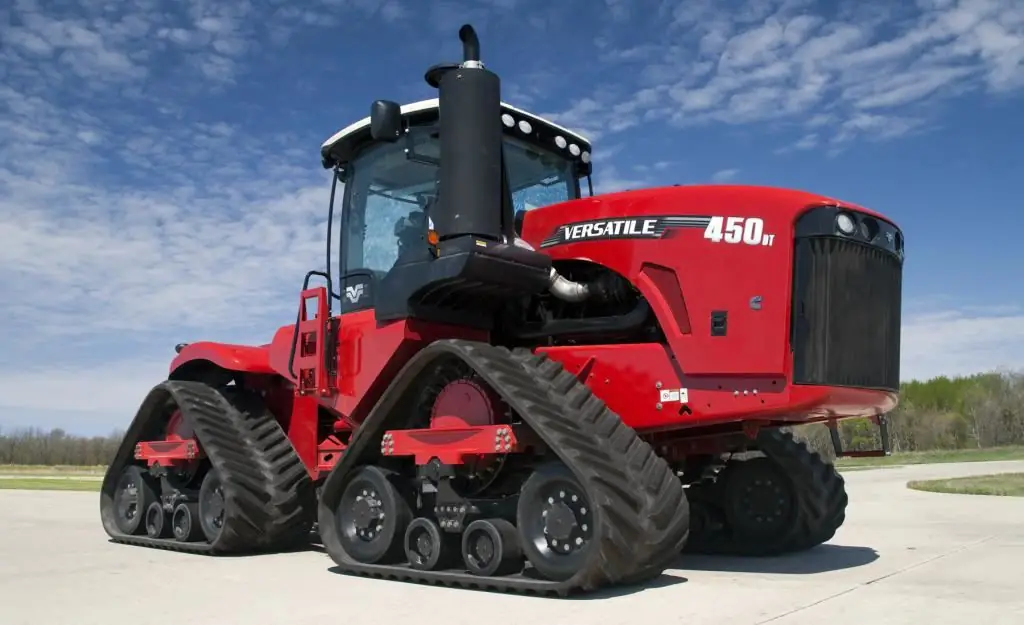
Büller brand tractors have proven their worth on the world market thanks to high-quality and reliable equipment. Buhler Druckguss AG took the lead in agriculture and industry a few years ago. The company's specialists introduce innovative technologies, so that customers can purchase reliable, economical and advanced equipment
"Toyota Tundra": dimensions, weight, classification, technical characteristics, declared power, maximum speed, operating features and owner reviews
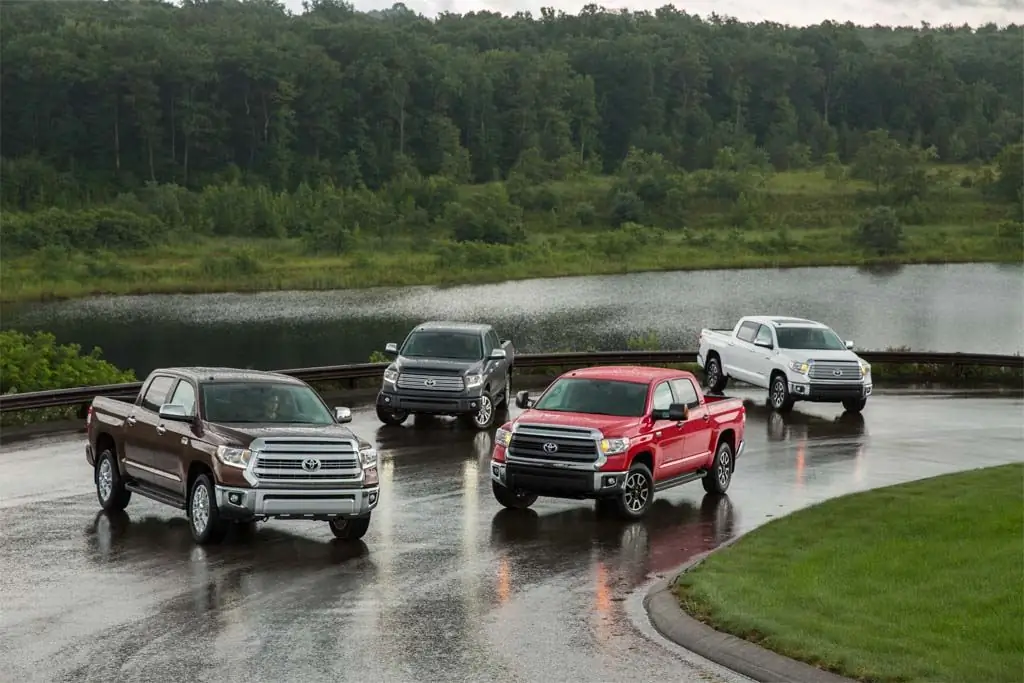
The dimensions of the Toyota Tundra are quite impressive, the car, more than 5.5 meters long and with a powerful engine, has undergone transformations and completely changed over the ten years of production by Toyota. In 2012, it was the Toyota Tundra that had the honor of being towed to the California Science Center Space Shuttle Endeavor. And how it all began, this article will tell
Starting the engine in the cold. Starting an injection engine in cold weather
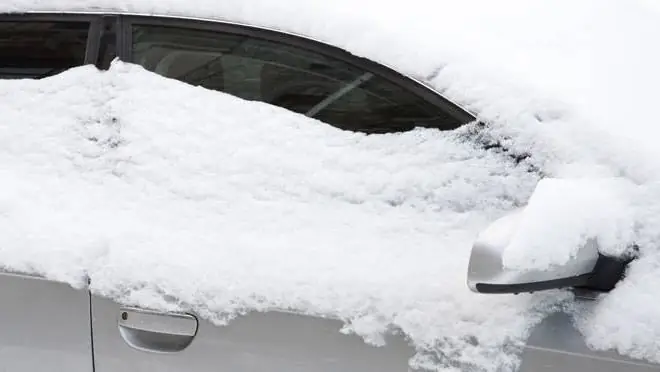
The article describes how to start the engine in cold weather. Considered injection and carburetor engines with specific examples and recommendations
Rolling stock of road transport: purpose, types, characteristics and operating rules
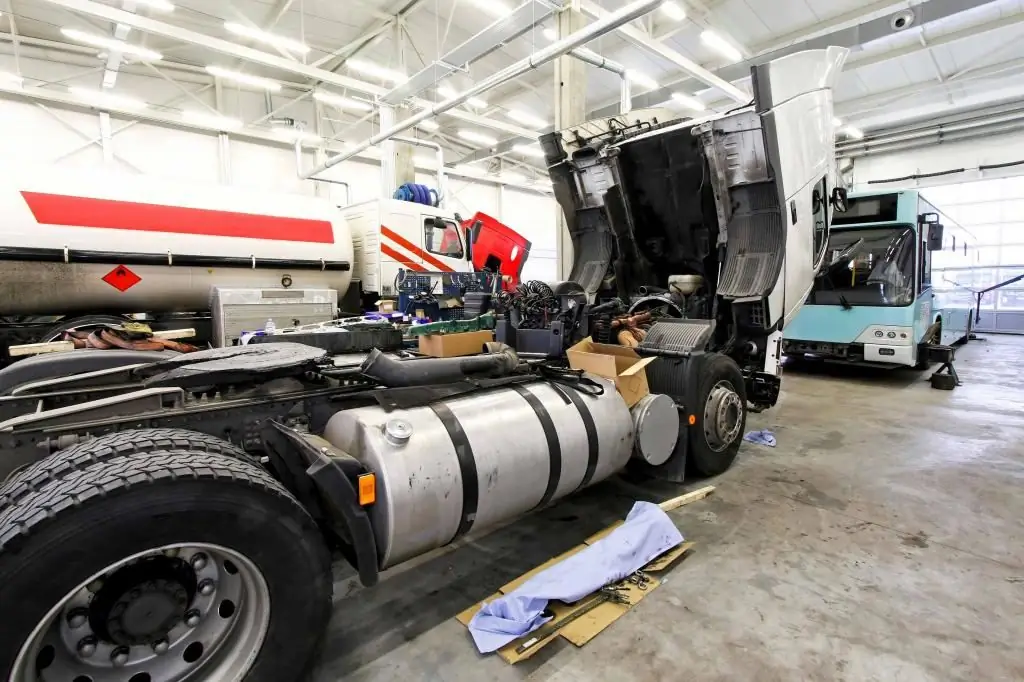
The concept of road transport rolling stock in a broad sense serves to determine the parameters of certain mechanisms that characterize them qualitatively. This is necessary for the correct selection of equipment in accordance with the conditions and specifics of the activity being carried out