2025 Author: Erin Ralphs | [email protected]. Last modified: 2025-01-22 21:14
With the development of ICE turbines, manufacturers are trying to improve their consistency with engines and efficiency. The most technically advanced serial solution is a change in the geometry of the inlet. Next, the design of variable geometry turbines, the principle of operation, and maintenance features are considered.
General Features
The turbines under consideration differ from the usual ones in the ability to adapt to the engine operating mode by changing the A / R ratio, which determines the throughput. This is a geometric characteristic of the housings, represented by the ratio of the cross-sectional area of the channel and the distance between the center of gravity of this section and the central axis of the turbine.
The relevance of variable geometry turbochargers is due to the fact that for high and low speeds the optimal values of this parameter differ significantly. So, for a small value of A/R, the flowhas a high speed, as a result of which the turbine spins up quickly, but the maximum throughput is low. Large values of this parameter, on the contrary, determine a large throughput and low exhaust gas velocity.
Consequently, with an excessively high A / R, the turbine will not be able to create pressure at low speeds, and if it is too low, it will choke the engine at the top (due to back pressure in the exhaust manifold, performance will drop). Therefore, on fixed geometry turbochargers, an average A / R value is selected that allows it to operate over the entire speed range, while the principle of operation of turbines with variable geometry is based on maintaining its optimal value. Therefore, such options with a low boost threshold and minimal lag are highly effective at high speeds.
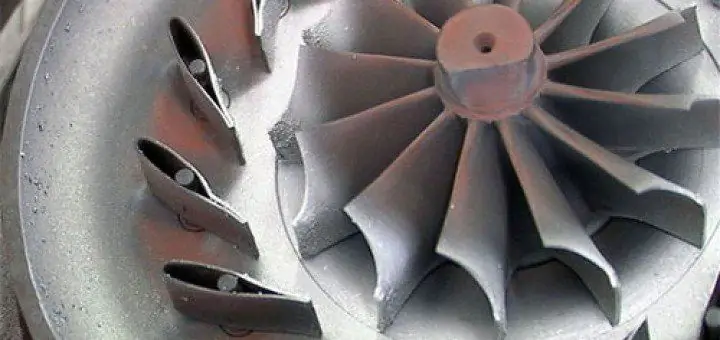
Besides the main name (variable geometry turbines (VGT, VTG)) these variants are known as variable nozzle (VNT), variable impeller (VVT), variable area turbine nozzle (VATN) models.
The Variable Geometry Turbine was developed by Garrett. In addition to it, other manufacturers are engaged in the release of such parts, including MHI and BorgWarner. The main manufacturer of slip ring variants is Cummins Turbo Technologies.
Despite the use of variable geometry turbines mainly on diesel engines, they are very common and gaining popularity. It is assumed that in 2020 such models will occupy more than 63% of the global turbine market. The expansion of the use of this technology and its development is primarily due to the tightening of environmental regulations.
Design
Variable geometry turbine device differs from conventional models by the presence of an additional mechanism in the inlet part of the turbine housing. There are several options for its design.
The most common type is the sliding paddle ring. This device is represented by a ring with a number of rigidly fixed blades located around the rotor and moving relative to the fixed plate. The sliding mechanism is used to narrow/expand the passage for the flow of gases.
Due to the fact that the paddle ring slides in the axial direction, this mechanism is very compact, and the minimum number of weak points ensures strength. This option is suitable for large engines, so it is mainly used on trucks and buses. It is characterized by simplicity, high performance at the bottom, reliability.
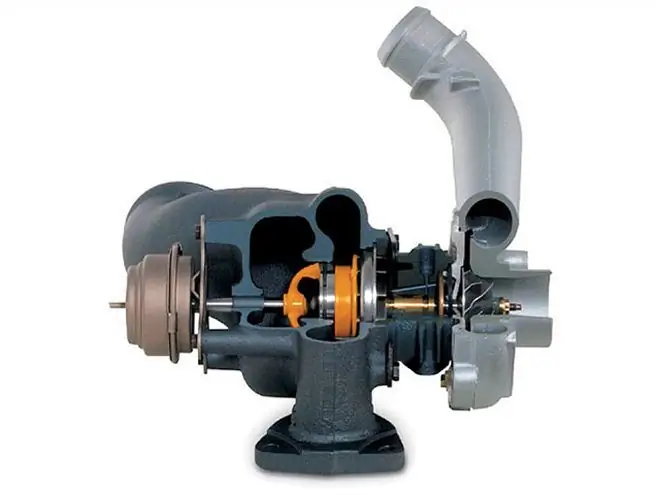
The second option also assumes the presence of a vane ring. However, in this case, it is rigidly fixed on a flat plate, and the blades are mounted on pins that ensure their rotation in the axial direction, on the other side of it. Thus, the geometry of the turbine is changed by means of the blades. This option has the best efficiency.
However, due to the large number of moving parts, this design is less reliable, especially in high temperature conditions. Markedproblems are caused by the friction of metal parts, which expand when heated.
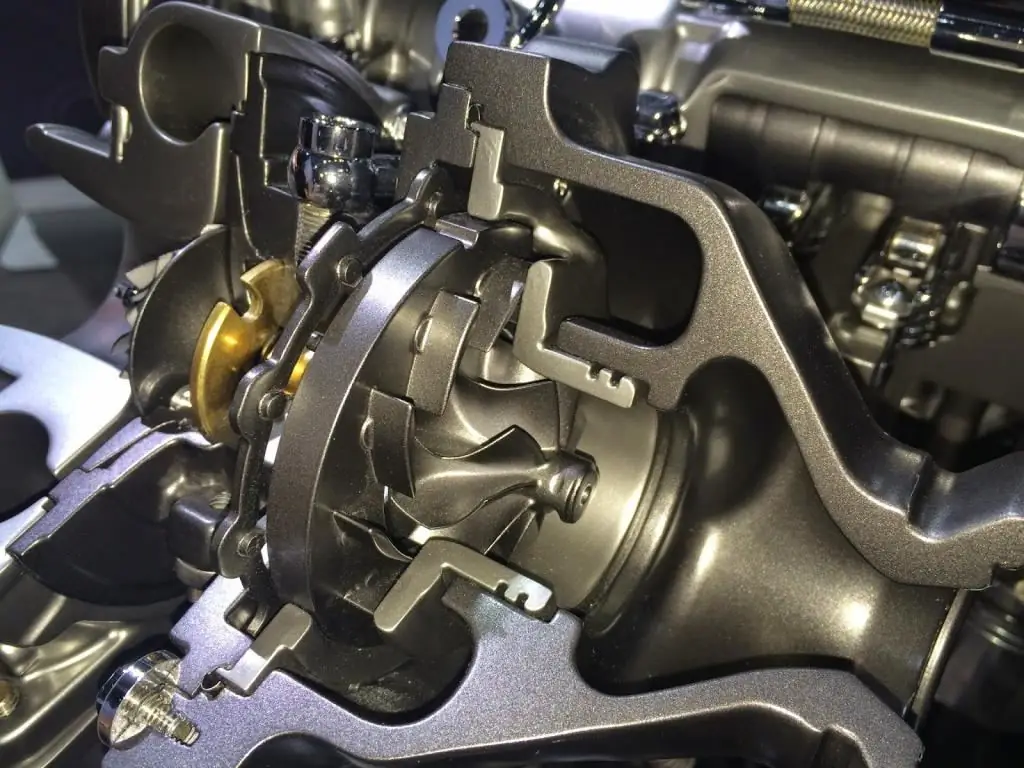
Another option is a moving wall. It is similar in many ways to the slip ring technology, but in this case, the fixed blades are mounted on a static plate instead of a slip ring.
Variable area turbocharger (VAT) has blades that rotate around the installation point. Unlike the scheme with rotary blades, they are installed not along the circumference of the ring, but in a row. Because this option requires a complex and expensive mechanical system, simplified versions have been developed.
One is the Aisin Seiki Variable Flow Turbocharger (VFT). The turbine housing is divided into two channels by a fixed blade and is equipped with a damper that distributes the flow between them. A few more fixed blades are installed around the rotor. They provide retention and flow merging.
The second option, called the Switchblade scheme, is closer to VAT, but instead of a row of blades, a single blade is used, also rotating around the installation point. There are two types of such construction. One of them involves the installation of the blade in the central part of the body. In the second case, it is in the middle of the channel and divides it into two compartments, like a VFT paddle.
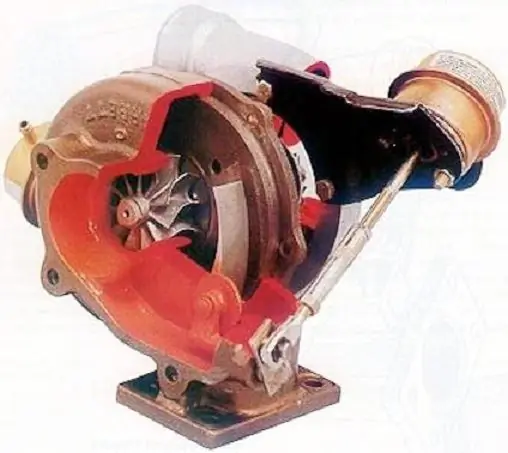
To control a turbine with variable geometry, drives are used: electric, hydraulic, pneumatic. The turbocharger is controlled by the control unitengine (ECU, ECU).
It should be noted that these turbines do not require a bypass valve, as due to precise control it is possible to slow down the flow of exhaust gases in a non-decompressive way and pass the excess through the turbine.
Operating principle
Variable geometry turbines work by maintaining the optimum A/R and swirl angle by changing the cross-sectional area of the inlet. It is based on the fact that the exhaust gas flow velocity is inversely related to the channel width. Therefore, on the "bottoms" for fast promotion, the cross section of the input part is reduced. With the increase in speed to increase the flow, it gradually expands.
Mechanism for changing geometry
The mechanism for the implementation of this process is determined by the design. In models with rotating blades, this is achieved by changing their position: to ensure a narrow section, the blades are perpendicular to the radial lines, and to widen the channel, they go into a stepped position.
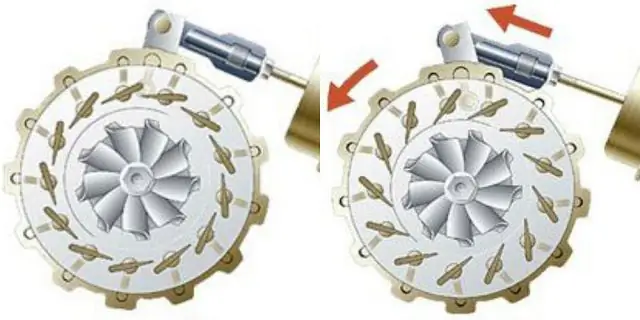
Slip ring turbines with a moving wall have an axial movement of the ring, which also changes the channel section.
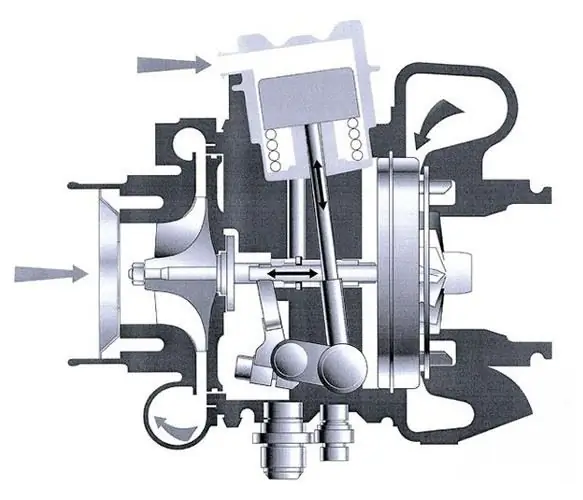
The principle of operation of VFT is based on flow separation. Its acceleration at low speeds is carried out by closing the outer compartment of the channel with a damper, as a result of which the gases go to the rotor in the shortest way. As the load increases, the damperrises to allow flow through both bays to expand capacity.

For VAT and Switchblade models, the geometry is changed by turning the blade: at low speeds it rises, narrowing the passage to speed up the flow, and at high speeds it is adjacent to the turbine wheel, expanding the throughput. Type 2 Switchblade turbines feature reversed blade operation.
So, on the "bottoms" it is adjacent to the rotor, as a result of which the flow goes only along the outer wall of the housing. As rpm increases, the blade rises, opening up a passage around the impeller to increase throughput.

Drive
Among the drives, the most common are pneumatic options, where the mechanism is controlled by a piston moving air inside the cylinder.
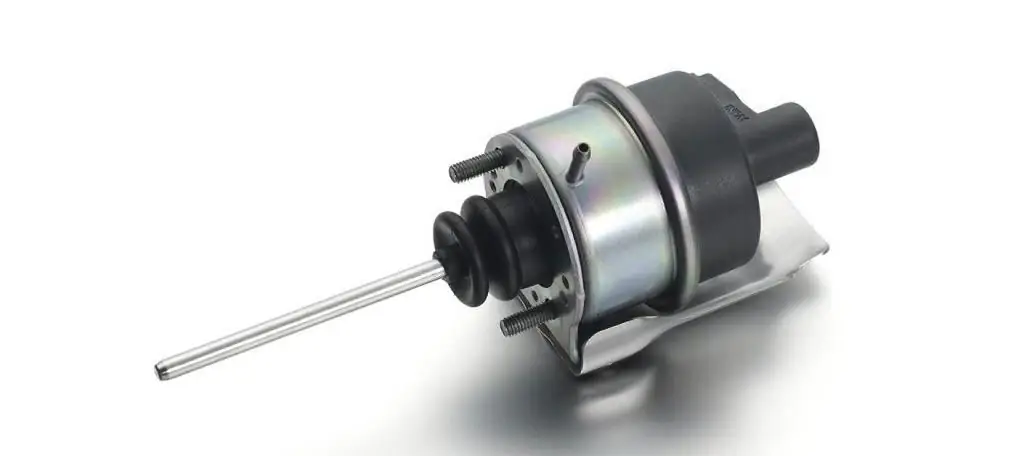
The position of the vanes is controlled by a diaphragm actuator connected by a rod to the vane control ring, so the throat can constantly change. The actuator drives the stem depending on the level of vacuum, counteracting the spring. Vacuum modulation controls an electric valve that supplies a linear current depending on the vacuum settings. Vacuum can be generated by the brake booster vacuum pump. The current is supplied from the battery and modulates the ECU.
The main disadvantage of such drives is due to the difficult to predict the state of the gas after compression, especially when heated. Therefore more perfectare hydraulic and electric drives.
Hydraulic actuators operate on the same principle as pneumatic actuators, but instead of air in the cylinder, a liquid is used, which can be represented by engine oil. In addition, it does not compress, so this system provides better control.
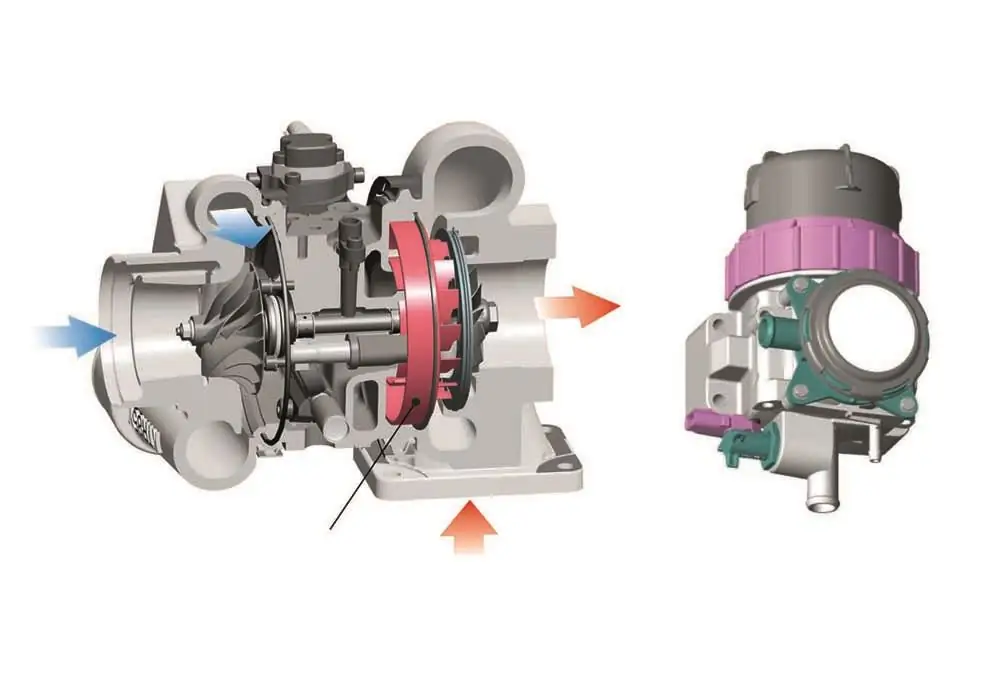
The solenoid valve uses oil pressure and an ECU signal to move the ring. The hydraulic piston moves the rack and pinion, which rotates the toothed gear, as a result of which the blades are pivotally connected. To transfer the position of the ECU blade, an analog position sensor moves along the cam of its drive. When the oil pressure is low, the vanes open and close as the oil pressure increases.
Electric drive is the most accurate, because the voltage can provide very fine control. However, it requires additional cooling, which is provided by coolant tubes (pneumatic and hydraulic versions use liquid to remove heat).
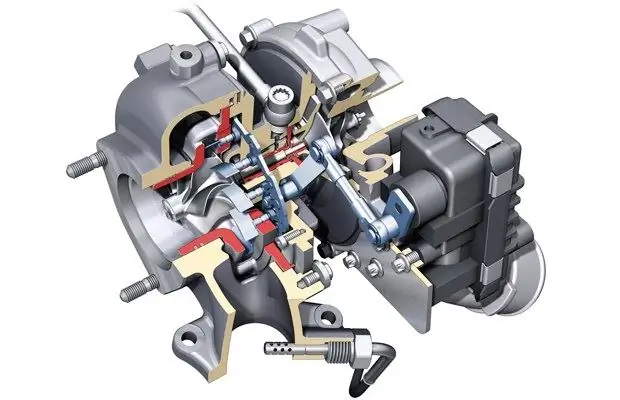
The selector mechanism serves to drive the geometry changer.
Some models of turbines use a rotary electric drive with a direct stepper motor. In this case, the position of the blades is controlled by an electronic feedback valve through the rack and pinion mechanism. For feedback from the ECU, a cam with a magnetoresistive sensor attached to the gear is used.
If it is necessary to turn the blades, the ECU providessupply of current in a certain range to move them to a predetermined position, after which, having received a signal from the sensor, it de-energizes the feedback valve.
Engine control unit
From the above it follows that the principle of operation of variable geometry turbines is based on the optimal coordination of the additional mechanism in accordance with the engine operating mode. Therefore, its precise positioning and constant monitoring is required. Therefore variable geometry turbines are controlled by engine control units.
They use strategies to either maximize productivity or improve environmental performance. There are several principles for the functioning of the BUD.
The most common of these involves the use of reference information based on empirical data and engine models. In this case, the feedforward controller selects values from a table and uses feedback to reduce errors. It is a versatile technology that allows for a variety of control strategies.
Its main drawback is the limitations during transients (sharp acceleration, gear changes). To eliminate it, multi-parameter, PD- and PID-controllers were used. The latter are considered the most promising, but they are not sufficiently accurate over the entire range of loads. This was solved by applying fuzzy logic decision algorithms using MAS.
There are two technologies for providing reference information: the average motor model and artificialneural networks. The latter includes two strategies. One of them involves maintaining boost at a given level, the other - maintaining a negative pressure difference. In the second case, the best environmental performance is achieved, but the turbine is overspeeding.
Not many manufacturers are developing ECUs for variable geometry turbochargers. The vast majority of them are represented by products of automakers. However, there are some third-party high-end ECUs on the market that are designed for such turbos.
General provisions
The main characteristics of turbines are air mass flow and flow velocity. Inlet area is one of the performance limiting factors. Variable geometry options allow you to change this area. So, the effective area is determined by the height of the passage and the angle of the blades. The first indicator is changeable in versions with a sliding ring, the second - in turbines with rotary blades.
Thus, variable geometry turbochargers constantly provide the required boost. As a result, engines equipped with them do not have the lag associated with the spin-up time of the turbine, as with conventional large turbochargers, and do not choke at high speeds, as with small ones.
Finally, it should be noted that although variable geometry turbochargers are designed to operate without a bypass valve, they have been found to provide performance gains primarily at low end, and at high rpm at fully openblades are not able to cope with a large mass flow. Therefore, to prevent excessive back pressure, it is still recommended to use a wastegate.
Pros and cons
Adjusting the turbine to the engine operating mode provides an improvement in all indicators compared to fixed geometry options:
- better responsiveness and performance throughout the rev range;
- flatter midrange torque curve;
- ability to operate the engine at partial load on a more efficient lean air/fuel mixture;
- better thermal efficiency;
- preventing excessive boost at high rpm;
- best environmental performance;
- less fuel consumption;
- extended turbine operating range.
The main disadvantage of variable geometry turbochargers is their significantly complicated design. Due to the presence of additional moving elements and drives, they are less reliable, and maintenance and repair of turbines of this type is more difficult. In addition, modifications for gasoline engines are very expensive (about 3 times more expensive than conventional ones). Finally, these turbines are difficult to combine with engines not designed for them.
It should be noted that in terms of peak performance, variable geometry turbines are often inferior to their conventional counterparts. This is due to losses in the housing and around the supports of the moving elements. In addition, the maximum performance drops sharply when moving away from the optimal position. However, the generalThe efficiency of turbochargers of this design is higher than that of fixed geometry variants due to the larger operating range.
Application and additional functions
The scope of variable geometry turbines is determined by their type. For example, engines with rotating blades are installed on the engines of cars and light commercial vehicles, and modifications with a sliding ring are used mainly on trucks.
In general, variable geometry turbines are most often used on diesel engines. This is due to the low temperature of their exhaust gases.
On passenger diesel engines, these turbochargers primarily serve to compensate for the loss of performance from the exhaust gas recirculation system.
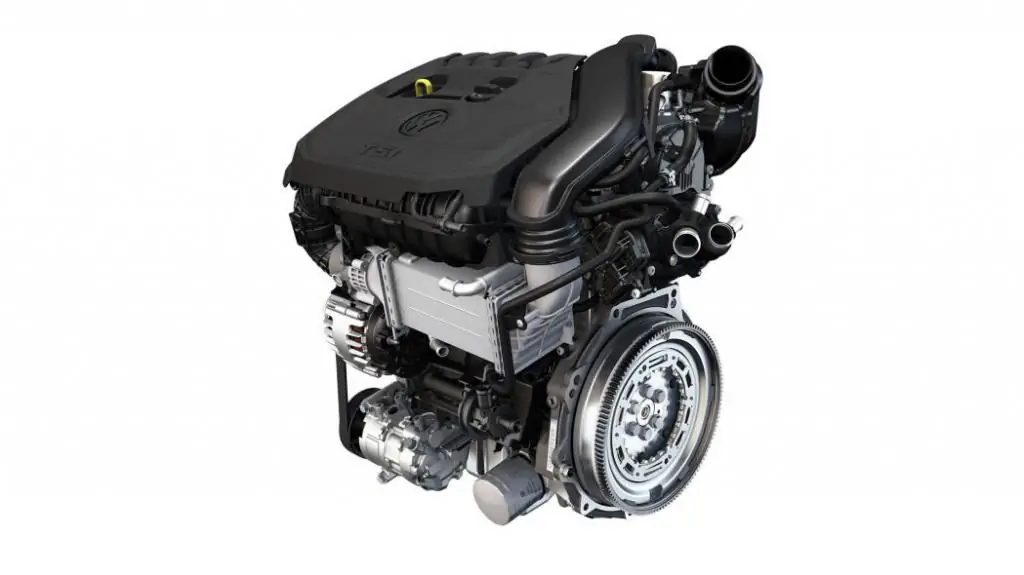
On trucks, the turbines themselves can improve environmental performance by controlling the amount of exhaust gases recirculated to the engine intake. Thus, with the use of variable geometry turbochargers, it is possible to increase the pressure in the exhaust manifold to a value greater than in the intake manifold in order to accelerate recirculation. Although excessive back pressure is detrimental to fuel efficiency, it helps to reduce nitrogen oxide emissions.
In addition, the mechanism can be modified to reduce the efficiency of the turbine in a given position. This is used to increase the temperature of the exhaust gases in order to purge the particulate filter by oxidizing the stuck carbon particles by heating.
Datafunctions require hydraulic or electric drive.
The noted advantages of variable geometry turbines over conventional ones make them the best option for sports engines. However, they are extremely rare on gasoline engines. Only a few sports cars equipped with them are known (currently the Porsche 718, 911 Turbo and Suzuki Swift Sport). According to one BorgWarner manager, this is due to the very high cost of producing such turbines, due to the need to use specialized heat-resistant materials to interact with the high-temperature exhaust gases of gasoline engines (diesel exhaust gases have a much lower temperature, so turbines are cheaper for them).
The first VGTs used on gasoline engines were made from conventional materials, so complex cooling systems had to be used to ensure acceptable service life. So, on the 1988 Honda Legend, such a turbine was combined with a water-cooled intercooler. In addition, this type of engine has a wider exhaust gas flow range, thus requiring the ability to handle a larger mass flow range.
Manufacturers achieve the required levels of performance, responsiveness, efficiency and environmental friendliness in the most cost-effective way. The exception is isolated cases when the final cost is not a priority. In this context, this is, for example, achieving a record performance on Koenigsegg One: 1 or adapting a Porsche 911 Turbo to a civilianoperation.
In general, the vast majority of turbocharged cars are equipped with conventional turbochargers. For high-performance sports engines, twin-scroll options are often used. Although these turbochargers are inferior to VGTs, they offer the same advantages over conventional turbines, only to a lesser extent, and yet have almost the same simple design as the latter. As for tuning, the use of variable geometry turbochargers, in addition to high cost, is limited by the complexity of their tuning.
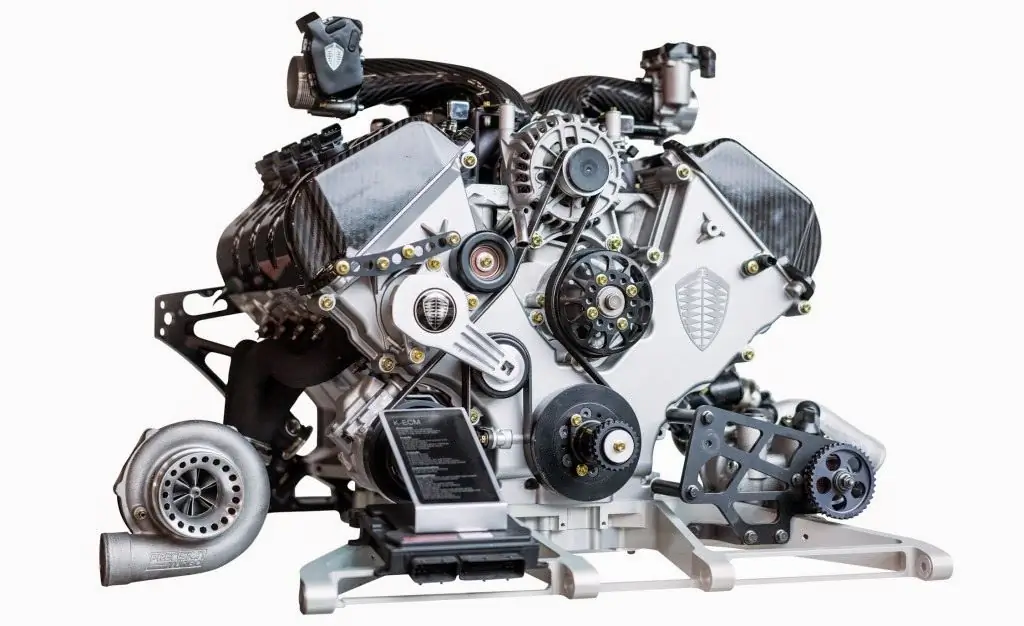
For gasoline engines, a study by H. Ishihara, K. Adachi and S. Kono ranked the variable flow turbine (VFT) as the most optimal VGT. Thanks to only one moving element, production costs are reduced and thermal stability is increased. In addition, such a turbine operates according to a simple ECU algorithm, similar to fixed geometry options equipped with a bypass valve. Particularly good results have been obtained when such a turbine is combined with an iVTEC. However, for forced induction systems, an increase in exhaust gas temperature by 50-100 °C is observed, which affects environmental performance. This problem was solved by using a water-cooled aluminum manifold.
BorgWarner's solution for gasoline engines was to combine twin scroll technology and variable geometry design into a twin scroll variable geometry turbine introduced at SEMA 2015. Hersame design as twin scroll turbine, this turbocharger has double inlet and twin monolithic turbine wheel, and is combined with twin scroll manifold, sequencing to eliminate exhaust pulsation for denser flow.
The difference is in the presence of a damper in the inlet part, which, depending on the load, distributes the flow among the impellers. At low speeds, all the exhaust gases go to a small part of the rotor, and the large part is blocked, which provides even faster spin-up than a conventional twin-scroll turbine. As the load increases, the damper gradually moves to the middle position and evenly distributes the flow at high speeds, as in a standard twin-scroll design. That is, in terms of the mechanism for changing the geometry, such a turbine is close to a VFT.
Thus, this technology, like variable geometry technology, provides a change in A / R ratio depending on the load, adjusting the turbine to the engine's operating mode, which expands the operating range. At the same time, the considered design is much simpler and cheaper, since only one moving element is used here, operating according to a simple algorithm, and heat-resistant materials are not required. The latter is due to a decrease in temperature due to heat loss on the walls of the double casing of the turbine. It should be noted that similar solutions have been encountered before (for example, quick spool valve), but for some reason this technology has not gained popularity.
Maintenance andrepair
The main maintenance operation for turbines is cleaning. The need for it is due to their interaction with exhaust gases, represented by the combustion products of fuel and oils. However, cleaning is rarely required. Intense contamination indicates a malfunction, which can be caused by excessive pressure, wear of gaskets or bushings of the impellers, as well as the piston compartment, clogging of the breather.
Variable geometry turbines are more sensitive to fouling than conventional turbines. This is due to the fact that the accumulation of soot in the guide vane of the geometry change device leads to its wedging or loss of mobility. As a result, the functioning of the turbocharger is disrupted.
In the simplest case, cleaning is carried out by using a special liquid, but manual work is often required. The turbine must first be disassembled. When detaching the geometry change mechanism, be careful not to cut the mounting bolts. Subsequent drilling of their fragments can lead to damage to the holes. Therefore, cleaning the variable geometry turbine is somewhat difficult.
In addition, it must be borne in mind that careless handling of the cartridge can damage or deform the rotor blades. If it is dismantled after cleaning, balancing will be required, but the inside of the cartridge is usually not cleaned.
Oil soot on the wheels indicates wear on the piston rings or valve group, as well as the rotor seals in the cartridge. Cleaning withouteliminating these engine malfunctions or repairing the turbine is impractical.
After replacement of the cartridge for turbochargers of the type in question, geometry adjustment is required. For this, persistent and rough adjusting screws are used. It should be noted that some models of the first generation were not initially configured by manufacturers, as a result of which their performance at the "bottom" is reduced by 15-25%. In particular, this is true for Garrett turbines. Instructions can be found online on how to adjust the variable geometry turbine.
CV
Variable geometry turbochargers represent the highest stage in the development of serial turbines for internal combustion engines. An additional mechanism in the inlet part ensures that the turbine is adapted to the engine operating mode by adjusting the configuration. This improves performance, economy and environmental friendliness. However, the design of the VGT is complex and the petrol models are very expensive.
Recommended:
Band brake: device, principle of operation, adjustment and repair
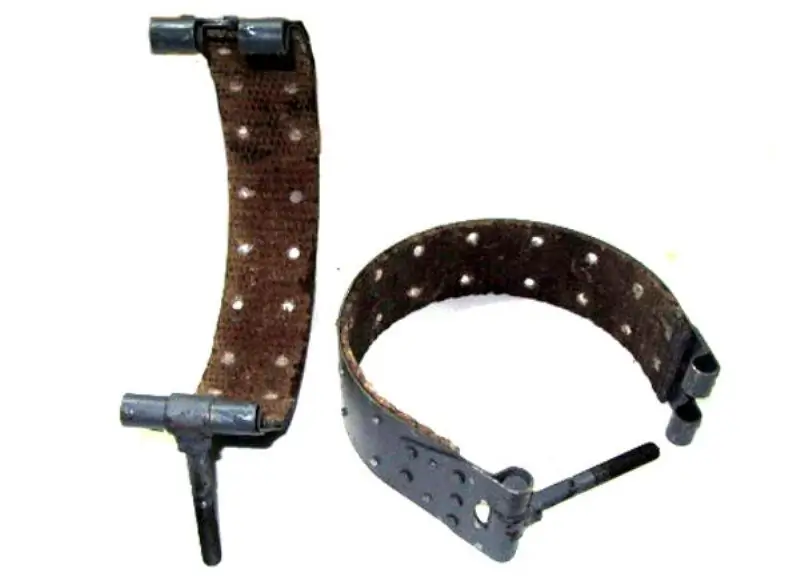
The brake system is designed to stop various mechanisms or vehicles. Another purpose is to prevent movement when the instrument or machine is at rest. There are several varieties of these devices, among which the band brake is one of the most successful
Parktronic constantly beeps: possible causes and repair. Parking radar: device, principle of operation
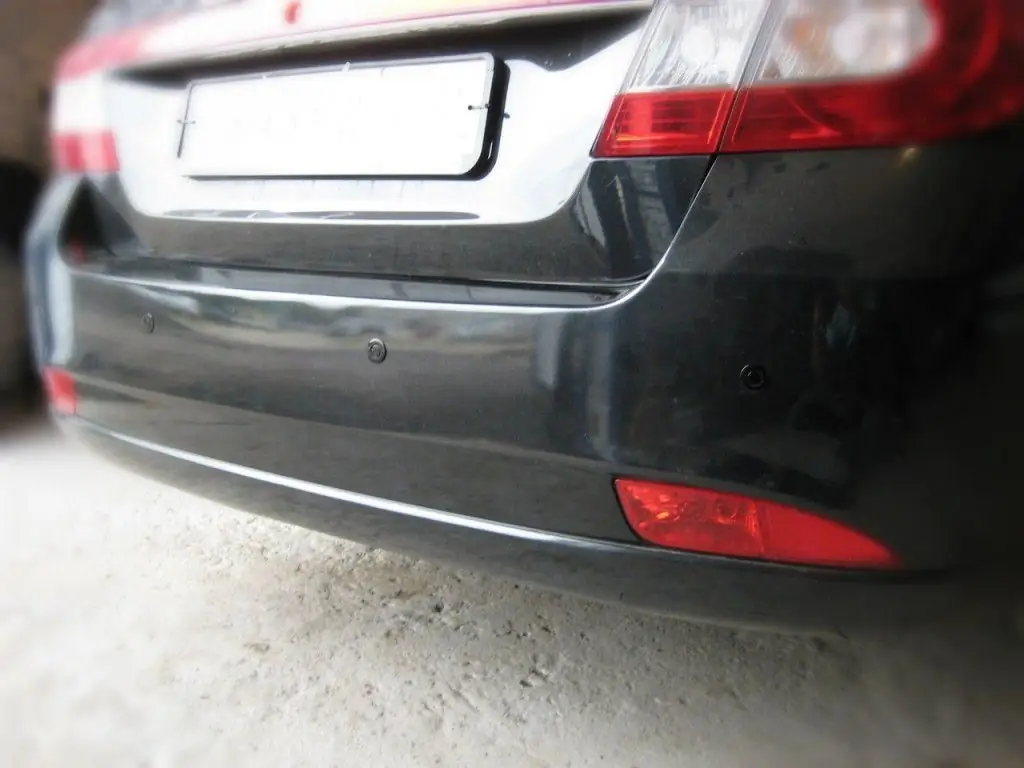
How to park without errors, avoiding an emergency? The question often arises not only among beginners on the road track, but also among experienced motorists. The fear of doing the wrong thing gets in the way, and manufacturers of various useful devices help get rid of it
Engine gas distribution mechanism: device, principle of operation, purpose, maintenance and repair
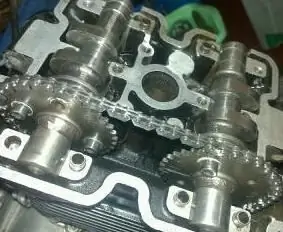
Timing belt is one of the most critical and complex components in a car. The gas distribution mechanism controls the intake and exhaust valves of an internal combustion engine. On the intake stroke, the timing belt opens the intake valve, allowing air and gasoline to enter the combustion chamber. On the exhaust stroke, the exhaust valve opens and exhaust gases are removed. Let's take a closer look at the device, the principle of operation, typical breakdowns and much more
The principle of operation of the variator. Variator: device and principle of operation
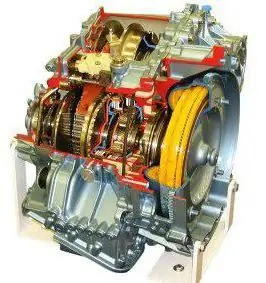
The beginning of the creation of variable programs was laid in the last century. Even then, a Dutch engineer mounted it on a vehicle. After such mechanisms were used on industrial machines
Planetary gearbox: device, principle of operation, operation and repair
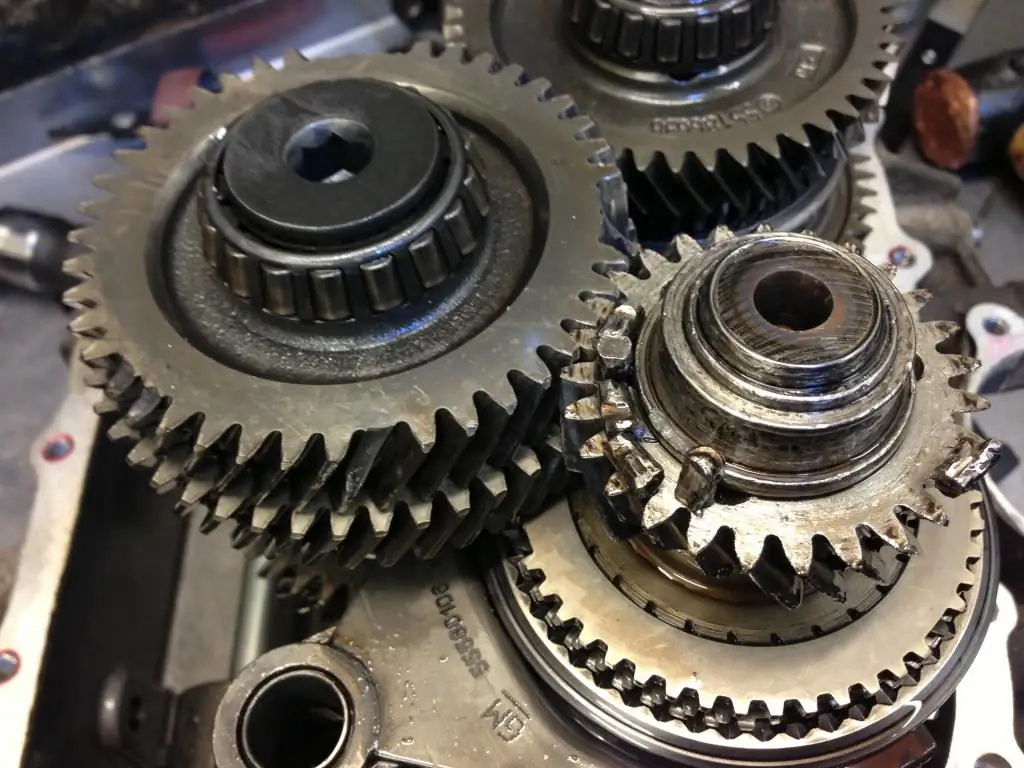
Planetary gears are among the most complex gear boxes. With a small size, the design is characterized by high functionality, which explains its widespread use in technological machines, bicycles and caterpillar vehicles. To date, the planetary gearbox has several design versions, but the basic principles of operation of its modifications remain the same